SMT制造商不断要求增加产量和提高精度,贴片机设备得以持续发展。并行贴装技术是新兴的贴片技术,其灵活性、产量及高正常运作时间可确保实现低价位的单位贴装成本。一种全新的平台建基于这些性能优势,其核心是在可扩展的多功能贴装部件上,为每个贴装头配置智能控制装置。这种分布式机器智能会对并行贴装技术的许多方面产生深远的影响。
激光对位技术
20世纪90年代激光技术研发用于CNC机器的工具对位,并迅速应用于贴装系统的元件对位。激光对位技术在并行贴装技术的发展过程中扮演了重要的角色,通过动态对位支持业内最高速度的射片 *** 作。该技术推出时,能够处理尺寸大至7 x 7mm的元件。
开发新型激光对位技术的驱动力来自于一个“梦想”,就是在单一平台上贴装种类更多元化的元件。这个目标已通过独立的传感器系统实现了,这种功能强大的贴装头机构重量更轻而散热更少 (这非常重要,因为热效应会严重影响精度),并具有高水平的抗电磁干扰(EMI)性能。它具有调整旋转速度的全新灵活性;新算法也已经推出,以扩大系统可处理元件形状的范围,包括用户定义元件形状。
这种独立型自校准多功能贴装头的优势依赖于先进的Firewire高带宽通信技术,该技术将传感器连接至控制单元。新型贴装头技术具有未来适用性,可通过现场固件升级来贴装创新元件。
第二代激光对位技术具有更高的性能,可处理更多不同类型的以元件或引脚外形为基本对位标准的元件,因此,只剩下很少的元件需要进行CCD视像检测。如今可采用激光技术对位的元件尺寸增至18 x 18mm,激光技术可识别更多的形状,精度也有显着提高。
在这种情况下,使用 激光对位技术能够减少精密贴装机的负荷,并有机会改善整个平台的元件平衡状况
电路板对位技术
以往,并行贴装技术使用一台专用电路板对位相机读取基准数据,由于这有可能引入电路板步进通过机器时产生的误差,所以通过定位板孔重新定位电路板是至关重要的,以确保每个元件的贴装精度达到要求。现在,每个贴装头均具备电路板对位能力,这对于电路板输送有着重要的意义。使用新型侧面夹紧系统,可在整个贴装系统中的任意电路板位置,以确定的精度进行快速产品转换。
此外,贴装头可在2分钟内转换,并且由于每个贴装头均针对高重复性机械接口进行校准,所以转换贴装头后无需校准即可恢复生产
Z轴上的置放力
由于每个贴装模块均具备智能和快速通信功能,所以可以重新评估Z轴置放力控制装置的可能性。原先的气动式Z轴运动执行器被伺服控制线性电机所取代,该电机可精确地控制高度,贴装力和挤压力。
现有多种可编程贴装力控制方法及新型挤压力控制算法,可防止元件发生微小破裂。自适应贴装算法可计入电路板的高度因素,以及每种元件的专用贴装力,从而提升高质量工艺的运作速度和产量。
伺服驱动能够精确地控制旋转运动,新型Z轴控制系统非常强大,具有很高的平均失效时间 (MTBF) 性能,有助于提高工艺可靠性和减少停机时间。
无差错贴装
由于每个贴装头均有自己的元件对位系统和控制器,它可进行局部吸嘴检查,使得 *** 作员无需打开机器,即可进行吸嘴位置和质量检测及诊断,并读出贴装头信息,如生产数据、利用率、轴向运动及旋转,并可能预测所需的维修 *** 作。
局部智能控制装置还能监控每个吸嘴的气动控制系统,检查步进后的送料带位置,确保小型元件正确地定位于吸嘴之下,以便可靠地拾取。吸嘴内的尘埃过滤器可防止系统污染。
这些新型贴装头功能带来了极佳的耐用性和灵活性,其正常运转时间长的特点对于降低单位贴装成本发挥了重要作用。
可满足所有贴装需求的单一平台
第二代激光对位技术的功能增强,可实现精确的可重复对位,使得一系列过往需要使用CCD相机的元件转用激光对位技术。现代工艺的发展使得许多IC可采用激光对位技术,未来元件制造商的合作将使该项功能进一步增长。
安必昂的小型AX架构贴片机能够处理多种元器件,这种机器也能根据生产需要,以低成本方式扩大产能,引入附加的CCD相机来处理大至25 x 25mm的元件。这种新型贴片平台的另一显着特点是,其AQ-1 精密贴装模块可处理所有其它 IC、先进封装元件和异形元件的。
结合AX架构与AQ-1模块的A系列平台取代了三项业内标准贴装概念,用户接口、运作、送料器,应用程序及维护具有共通性。因此,新平台看上去像单一机器,其精度高达4 δ级别的25微米,灵活的贴装头可处理300多种编号的元器件,还可在整个平台内进行优化以实现最大化产量。
欢迎分享,转载请注明来源:内存溢出
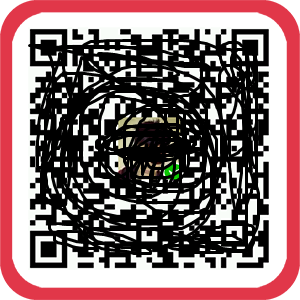
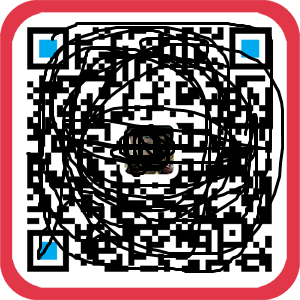
评论列表(0条)