本文介绍,一个电子制造服务(EMS)提供商怎样评估与实施自动光学检查(AOI)。
印刷电路板(PCB, Printed Circuit Board)制造商不断地面临测试与检查的挑战。电路板密度的增加挑战着传统的针床(bed-of-nails)在线测试(ICT, in-circuit test)以及 *** 作员的视觉检查。改变电路板的尺寸大小提出更多的挑战,因为它使手工检查更加困难。为了对这些发展作出反应,越来越多的制造商开始评估自动光学检查(AOI, automated opTIcal inspecTIon)作为一个解决方案。
AOI策略
在大批量和高复杂性的制造环境中,装配线上每个 *** 作员工位的占地面积都代表着一个特殊的价值。对此,电子制造服务(EMS)提供商*希望检查技术可以防止“漏网之鱼”走出工厂,提高产品品质。因此,该公司将AOI作为一个工具,来帮助装配线生产出持续的高品质电路板。
通过使用AOI作为减少缺陷的工具,在装配工艺过程的早期查找和消除错误,该公司预期得到几项利益:
早期发现缺陷将避免将坏板送到随后的装配阶段
AOI将减少修理成本
将避免报废不可修理的电路板 表一、AOI 在装配线上检查什么检查顶面回流焊接元件检查波峰焊接前通孔元件检查波峰焊接之后的通孔及SMT元件检查压入配合之前的连接器引脚检查压入配合之后的连接器引脚
在装配线中使用AOI
表一解释了AOI在该装配线上检查什么。对该制造商,AOI系统及其传送带是制成一体的,因此通过检查的板可连续地通过装配线。可是,如果发现失效的板,它被传送到第二条传送带,返回到 *** 作员工位进行修理。在该制造商那里,AOI提供全面的缺陷覆盖,同时满足每块板2 - 2.5分钟的装配线速度。
特别有帮助的是,该系统可以在施加全部装配压力之前发现高密度压力配合连接器的不对准的引脚。由于连接器容易不对准,在部分压入之后、完全压入之前,AOI检查这些1000个引脚单元,看其引脚尖是否到了通孔内。如果这时发现折弯的或不见的引脚,还可以进行修理。在最后压入之后的第二次检查确认装配的完整性。这里,AOI用作缺陷预防与检查工具。
在该制造商的情况中,AOI系统补充ICT与功能测试。通过在电气测试之前扫描电路板,AOI从装配过程发现缺陷,提高电气处理或功能测试阶段的合格率(例如,焊接品质问题,不可测试的元件,元件位置错误),减少工厂的“漏网之鱼”。
连接器压入是最后的装配步骤。如果连接器引针在压入期间弯曲,装配就全部损失。通过防止该类缺陷的发生,AOI系统降低报废成本。
AOI与人工检查比较
在 AOI 之前,由人工 *** 作员来完成电路板的检查。该过程涉及许多 *** 作员在装配线的工位上,使用显微镜和电路板覆盖图来找出丢失的元件、错误的贴放位置和焊接缺陷。检查板是通过四分区的程序,即,每个工位负责检查板的四分之一。虽然检查小板相对容易,但是随着板的尺寸增加到18"x20",成千个元件在上面,这项工作很快变成繁重的体力负担。因为检查最重要的因素是准确性与可*性,所以甚至在最好的环境中,手工检查都有其局限性。
对这个EMS提供商,人工检查的进一步挑战就是时间。每一个检查工位必须产生连续的板流,满足装配线的“节奏”,以保持持续性。如果一个工位被耽误,它将影响整个装配线。并且对较大的板,检查时间增加到视觉品质评估简直无法保持生产线速度的地部。最后,需要雇佣更多的 *** 作员来处理较大的板造成额外的人工成本和人力资源问题。
AOI与X光检查比较
该公司使用X光检查来完成诸如球栅阵列(BGA)检查的任务,作为ICT的补充。可是,考虑到自动检查方案,X光被排除了,因为它不能满足电路板尺寸、厚度、重量和周期时间的要求。需要的是一台可以在压入之前检查通孔中元件引脚的机器。
欢迎分享,转载请注明来源:内存溢出
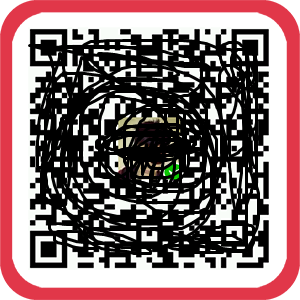
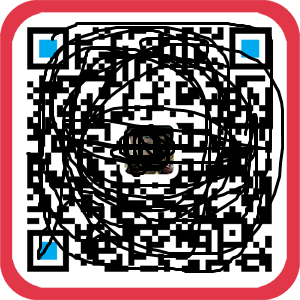
评论列表(0条)