Same? Really the Same? Maybe? The Cross-Reference Challenge
Abstract: Parts cross-reference charts are created because customers want second sources to protect them from supply shortages and high prices. This applicaTIon note discusses pitfalls to avoid with industry-standard parts and why parts “crosses” must be applicaTIon specific. The arTIcle will explain why a part can work well in the majority of applicaTIons, but fail in your specific application. Also defined is the only method to ensure compatibility between parts from two manufacturers.
Industry-Standard PartsTwo IC companies cooperate to try to make exact second-source parts by using the same mask set. The parts start out to be the same, however, they can drift apart as the two manufacturing processes inevitably change. Since the part differences may be very subtle, industry-standard part numbers do not ensure complete device interchangeably in every application.
Industry-standard parts using the same part number are usually different parts designed by different design engineers. To someone without experience, the parts can look the same. Someone may say that the parts are the same because they have similar pinouts. For example in Figure 1, a race car and an electric automobile are the same because they share four tires and a steering wheel. But these vehicles are not the same because they are designed for drastically different applications. Some race cars only make left turns; they have proficient drivers and pit crews to change tires to match track conditions such as rain and temperature. The average person might afford an economical car, drive it themselves, and get it serviced locally. Same or different? We have to admit that it is more exciting to watch a professional car race, and that these cars are really very different.
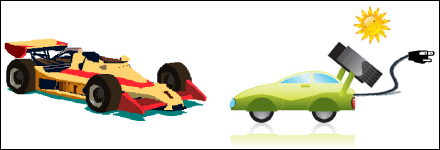
Figure 1. Race cars and electric cars are the same, and different at the same time.
Let History Tell the StoryHere are a few examples, sadly based on true stories, and "only the names have been changed to protect the innocent."
Some years ago a company had a frequency-modulated (FM) signal path that required a limiter. To save cost the circuit designer found a logic part that did the job. The Bill of Materials called out a single manufacturer's part and the product went into production. After several months of successful production, suddenly every system was failing, bringing the production line to a crashing halt. Panic ensued. Finally, the original circuit-design engineer was consulted. He took one look at the spectrum analyzer and ripped the PC board out of the machine. He pointed to the logic part and screamed, "Why do we bother to provide documentation, if production ignores the print?" The single manufacturer's part had symmetrical rise and fall times. Other manufacturers' parts had slow rise times and fast fall times. The parts salesman had said that the parts were "pin-for-pin compatible" and that the alternative was less expensive. (The parts were interchangeable in most logic circuits, but not in an FM limiter). The production buyer had decided to save the company money; the alternative "compatible" part had been purchased. Obviously management control was lax and the money-saving move had the opposite effect.
One must beware of pin-for-pin compatible parts. In another case, two manufacturers made phase-lock-loop (PLL) ICs. They were widely touted as pin-for-pin compatible. The pins all had the same names and the parts were both good PLLs. Unfortunately, the external components required to set the center frequency were different. If a designer used the wrong part in the circuit, it did not work as expected.
In yet another situation, a manufacturer replaced an older IC with an improved part that was "better." The new part had the same part number, a wider bandwidth, and was less expensive. Sales thought everyone would like it—after all they were getting something for nothing. What an easy part to sell and sell they did, until circuits that had been functioning well for years in the customer's basic, bread-and-butter products started failing. As parts were returned to the factory, sales came to the jarring realization that many of the customers' circuits were designed to take advantage of the old part as a natural lowpass filter. Those circuits needed the part to have the original lower bandwidth. The "something for nothing," i.e., the greater bandwidth, was actually more costly, did not fit some applications, and was ultimately bad.
A number of years ago, this problem was so bad in one company, that the engineers started adding a line to the title block of the parts drawings. Designed to look like a military specification, it said "MIL TP41." Products went into production for about a year before anyone questioned the notation. The note means, "Make it like the print for once."
Evaluating Pin-for-Pin Compatible PartsMaxim has a voltage reference, the MAX6195, which has a pinout that seems to match a competitor's part. This is one of those, "Yes, the parts are almost the same, but..." cases. If we set up the background conditions, we can explain the real difference between these parts.
A series voltage reference is like a low-dropout linear voltage regulator, but is more accurate, See Figure 2. An internal servo control loop is used to regulate the output voltage. The output voltage is compared to an internal bandgap voltage, and the output is controlled to the required accuracy over the temperature specification. Therefore, the output node of a voltage reference is the feedback node used to control the output specifications and stability.
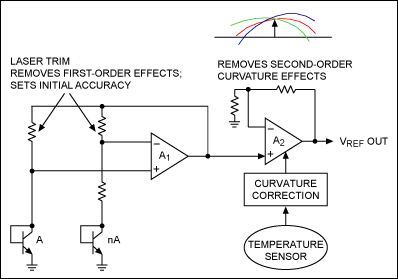
Figure 2. A simplified diagram of a typical voltage reference.
Op amp A1 compares two currents, one with a positive temperature coefficient and one with a negative temperature coefficient that makes up the bandgap reference. Op amp A2 provides gain with feedback from the output, as well as correction of temperature curvature. This illustrated "typical" reference is greatly simplified. The MAX6195 data sheet reveals that the device is actually comprised of 70 transistors.
During the IC design phase a part's output requirements are defined. As with many things in the engineering discipline, trade-offs are necessary. One specification may be improved and another relaxed to optimize a part for the target application. What is important to one customer might not be critical for another. Thus design goals and market objectives are set as a series of compromises.
With the MAX6195, Maxim chooses to produce a voltage reference that has a lower cost of ownership. The MAX6195 is designed so that large expensive, multiple-output capacitors are not necessary. A competitor takes the opposite route and recommends four external capacitors. This is not a case where one approach is good and the other is bad. Rather, different applications have different requirements.
The competitive part requires at least a 1µF output capacitor to meet specifications. The competitor recommends that four capacitors be used, two on the input (10µF and 0.1µF in parallel) and two on the output (1µF and 0.1µF in parallel). The MAX6195 data sheet says that all capacitors are optional.
The documentation for both the competitive and Maxim voltage references discuss the addition of capacitors for transient response improvement. The MAX6195 data sheet states;
Output/Load CapacitanceThe competitor recommends the large electrolytic capacitors (1µF to 10µF) for stability and the parallel 0.1µF capacitors to improve transient response.
Devices in this family do not require an output capacitance for frequency stability. They are stable for capacitive loads from 0 to 2.2nF. However, in applications where the load or the supply can experience step changes, an output capacitor will reduce the amount of overshoot (or undershoot) and assist the circuit's transient response. Many applications do not need an external capacitor, and this family can offer a significant advantage in these applications when board space is critical.¹
Really, why are the devices different?
Engineering is about compromise. Specifications for most things can, and are tilted to favor some parameter. A part optimized for a certain application will be skewed in a different way compared to a part for another application. In this instance the two parts are defined with different objectives, much as the race car and environmentally-friendly cars of Figure 1. The MAX6195 requires no capacitors; the competitor's part requires at least 1µF in capacitance. If the application requires better transient response, the Maxim part requires one small capacitor. Meanwhile, the competitor recommends four capacitors and one of those capacitors may be as big as 100µF.
How to Be Assured that the Cross-Referenced Part Will Really WorkIs it surprising that we can get a race car or an electric car when we just specify a "car?" As a matter of fact, we would be angry if that was not so. After reading all the brochures and data sheets, what do we as the automobile buyer do? We take a test drive.
The same approach should apply when specifying cross-referenced IC parts. After reading the data sheet and running an evaluation on the bench, experienced customers will actually have a competent engineer try the replacement part in the target socket. The engineer approves the new part for production use only after through testing.
This is the only way to be sure that the part works in a specific application.
欢迎分享,转载请注明来源:内存溢出
评论列表(0条)