As higher levels of power dissipaTIon underscore the need for cooling (especially for processors), more and more fans are finding their way into small electronic enclosures. The dust pulled into these enclosures by fans, however, can cause major problems for high reliability systems. By coaTIng heat sinks and electrically charged components, it acts as a blanket that raises the effective thermal impedance between those components and the air.
A simple way to combat this problem is to place a disposable filter on the air intake. If the user fails to replace the filter on a regular basis, however, it can become clogged and act as an air dam. That condition is worse than the original problem. Trying to sense a clogged filter by sensing the fan rotation with tachometer signals is useless, because fan rotation is not directly related to airflow.
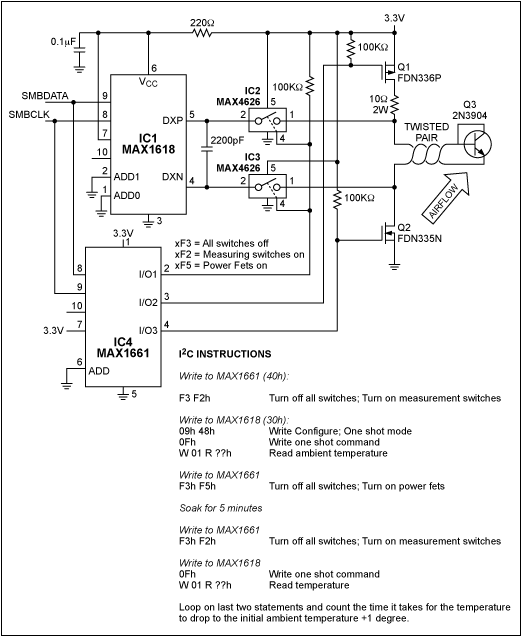
Figure 1. By heating a temperature-sense element (Q3) and then noting the time for it to return within 1°C of its original temperature, this anemometer measures the rate of airflow.
Using SMBus I/O expander IC4, turn off MOSFETs Q1 and Q2, and turn on the analog switches IC2 and IC3. Measure the ambient-air temperature with no preheating on Q3. Then, to apply current for heating Q3, turn off IC2 and IC3, and turn on Q1 and Q2. Allow an approximate five-minute "soak" to reach temperature equilibrium. (The exact heating time necessary for equilibrium depends on the setup, and must be determined by experiment.)
When equilibrium is attained, remove power from Q3 by turning off Q1 and Q2, and turn on the analog switches IC2 and IC3 to make temperature measurements. Airflow is directly related to the rate at which the temperature drops, and can be determined by noting the time required for the transistor to return to within 1°C of its original temperature.
The temperature sensor injects a very small current into the base junction, so layout is important to keep noise off the DXP and DXN lines. If the remote transistor is to be mounted in an air channel, the use of a twisted-wire connection will allow distances up to 12 feet. The following table lists airflow vs. cooling time for a sensor placed about 12 inches away from a fan running at full speed (12V), at medium speed (8V), at low speed (6V) and zero speed (off).
Longer power-soak times, (up to 30 minutes), do not alter these values significantly.
The circuit draws about 200mA when Q3 is heating. If this power dissipation is a problem, one can lower the frequency of measurement to hourly or even daily cycles, because changes in airflow occur slowly over time. Measurements can also be scheduled during times of low system activity, when the overall power use is down.
A similar version of this article appeared in the August 30, 2001 issue of EDN magazine.
SMBus is a trademark of Intel Corp.
欢迎分享,转载请注明来源:内存溢出
评论列表(0条)