Since their invention a few years ago, white light-emitting-diodes (LEDs) have been steadily gaining in popularity. Because they offer whiter light than incandescent bulbs and are easier to use than fluorescent tubes, they have been steadily gaining market share in a variety of lighting applications such as flashlights and display backlighting in handheld electronics. However, white LEDs present their own set of technical issues.
The most obvious issue when using white LEDs is that they are somewhat poorly matched. As an example, a typical white LED specification for forward voltage, Vf, at 20mA may read 3.0V minimum, 3.5V typical, and 4.0V maximum. Obviously, a constant voltage source is not the solution. Although the recommend means of achieving matched brightness is to drive each LED with the same amount of current, this can be expensive; therefore, most applications simply use a fixed bias voltage and ballast resistors, as seen in Figure 1.
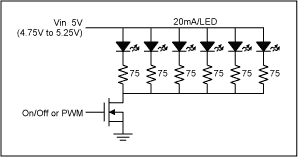
Figure 1. Most applications simply use a fixed bias voltage (5V in this case) and ballast resistors (75Ω in this case) to achieve approximate white LED brightness matching.
When designing a circuit like Figure 1, usually fairly good brightness matching is achieved. However, as most people involved with mass production know, products coming off an assembly line one after the other exhibit fairly uniform characteristics, but over the course of production, there may be substantial lot-to-lot variation. This, of course, applies to the white LEDs. Typically a production headache ensues wherein each new batch of LEDs needs to be characterized and a different ballast resistor value chosen. If multiple white LED suppliers are used, the problem is further exacerbated. To demonstrate this, three white LEDs from each of three manufacturers were purchased and tested using the circuit of Figure 1. Brand A was purchased from the leading white LED manufacturer, and the LEDs arrived in a small plastic bag. Brand B was purchased from the second leading white LED manufacturer, and the LEDs arrived on tape. Brand C, from a smaller manufacturer, was purchased at a local electronics store, and the LEDs were individually packaged. The results are tabulated in Table 1. To evaluate the manufacturability of the circuit of Figure 1, three white LEDs from each of three manufacturers where purchased and the LED currents measured. Note that brand-to-brand matching is poor, as seen by the 3.27mA standard deviation of the averages.
Table 1.
As can be seen by the "Stdev" standard deviation column of Table 1, the matching within each brand is fairly good. In fact, Brand A and Brand B exhibit very good matching. As might be expected, the individually packaged LEDs of Brand C have slightly looser matching. A figure-of-merit for within-the-brand matching, 0.54mA, is obtained by taking the average of the standard deviations.
As can be seen by the "Avg" average column of Table 1, the brand-to-brand matching is fairly poor. Brand A draws the most current (24.6mA average), while Brand B draws the least (18.3mA average). A figure-of-merit for brand-to-brand matching, 3.27mA, is obtained by taking the standard deviation of the averages.
As stated earlier, solutions that regulate individual LED current, or at least one LED's current, will provide better lot-to-lot and brand-to-brand matching over the manufacturing life of the product. However, these solutions usually require fairly expensive ICs. Thankfully, if cost is of more concern than perfect matching, an inexpensive low-dropout (LDO) linear regulator can provide enough of a benefit to avoid tweaking the ballast resistor value with each new batch of LEDs. Figure 2 shows how to use the LDO in an in-between voltage and current regulation mode, which automatically varies the bias voltage in response to the forward voltage of one of the LEDs.
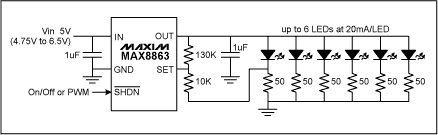
Figure 2. By adding an inexpensive LDO to make the bias voltage automatically variable, brightness matching over white LED lot-to-lot and/or brand-to-brand variation will be substantially improved.
To demonstrate the benefits of Figure 2, the same three LEDs from each of three manufacturers where tested again with results tabulated in Table 2. Although there is a small compromise in within-the-brand matching (0.77mA vs. 0.54mA for Table 1), the brand-to-brand matching is 340% improved (0.96mA vs. 3.27mA for Table 1)! To evaluate the matching performance of the circuit of Figure 2, the same three batches of three white LEDs were tested again. Note that brand-to-brand matching is much improved, as seen by the 0.96mA standard deviation of the averages vs. 3.27mA from Table 1.
Table 2.
Note that the LDO in Figure 2 needs to be an externally adjustable type, such as the MAX8863, which has a 1.25V feedback threshold (Vset). Also, the size and cost of adding a small SOT-23 packaged LDO is partially offset because the LDO has a shutdown pin, making the N-channel FET of Figure 1 no longer required for on/off or PWM dimming control. The LDO provides other advantages, as well, such as LED short-circuit protection, a wider input supply voltage range, and PSRR in cases where the 5V supply is shared by other circuits. Furthermore, the Brand A LEDs no longer run "hot", reducing power dissipation stress concerns.
Figure 3 shows how to modify Figure 2 for 15mA per LED, as required by most portable backlighting applications using surface mount white LEDs. The MAX8863 will support up to 8 LEDs at 15mA per LED. Because the forward voltage of the LEDs and the voltage across the ballast resistors will be less at 15mA, the minimum input voltage is also lower.
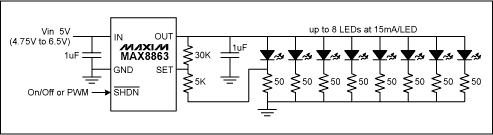
Figure 3. The MAX8863 LDO can drive from one to 8 white LEDs at 15mA per LED with good brightness matching despite LED lot-to-lot or brand-to-brand variations.
欢迎分享,转载请注明来源:内存溢出
评论列表(0条)