Semiconductor components that use new signal processing techniques for piezoresistive pressure sensors have enabled precise, automatic, and low-cost electronic compensation of the standard error parameters. The resulting simplification and convenience have opened a wide field of new applications, including the use of bridge sensors for properties other than pressure.
Because most control systems operate with electrical signals, pressure or force must be converted to current or voltage before further processing or analysis. Capacitive and resistive signal transducers are commonly used for this purpose. Capacitive sensors detect pressure as a capacitance associated with the distance between two (or more) diaphragms, which changes in response to a change in pressure. To provide useful output, this capacitance change is usually expressed as attenuation of an AC signal or as a frequency shift in a resonant circuit.
In resistive sensors, pressure changes the resistance by mechanically deforming the sensor, enabling the resistors in a bridge circuit, for example, to detect pressure as a proportional differential voltage across the bridge. Conventional resistive pressure measurement devices include film resistors, strain gauges, metal alloys, and polycrystalline semiconductors.
Monocrystalline silicon pressure sensors have come into wide use in recent years. Though manufactured with semiconductor technology, they also operate on the resistive principle. The resistance change in a monocrystalline semiconductor (a piezoelectric effect) is substantially higher than that in standard strain gauges, whose resistance changes with geometrical changes in the structure. Conductivity in a doped semiconductor is influenced by a change (compression or stretching of the crystal grid) that can be produced by an extremely small mechanical deformation. As a result, the sensitivity of monocrystalline sensors is higher than that of most other types. Specific advantages are:
- High sensitivity, > 10mV/V
- Good linearity at constant temperature
- Ability to track pressure changes without signal hysteresis, up to the destructive limit
- Strong nonlinear dependence of the full-scale signal on temperature (up to 1%/kelvin)
- Large initial offset (up to 100% of full scale or more)
- Strong drift of offset with temperature
Manufacturing Piezoresistive Pressure SensorsFor optimal application of these sensors, the user needs to understand their structure, their properties, and how they are made. Monocrystalline silicon in a wafer format provides very high mechanical strength and elastic behavior up to the point of mechanical breakdown, yielding sensors that exhibit only minor response to mechanical aging and hysteresis.
Anisotropically etching the back of a silicon wafer to create round (or square) holes that stop just short of the front surface produces silicon diaphragms with areas up to 7mm × 7mm, and thicknesses measuring 5-50 microns, ±1 micron (see Photo 1). The size and thickness of the finished diaphragm depend on the pressure range desired.
Photo 1. Anisotropic etching achieves extreme precision in fabricating mechanical structures such as the pressure sensor diaphragm shown here in cross section.
Deformation by applied pressure causes high levels of mechanical tension at the edges of the diaphragm. Semiconductor resistors on the front side transduce this tension into resistance changes by means of the piezoresistive effect. Positioning the resistors in this area of highest tension increases sensitivity but at the same time introduces problems. Misregistration of resistors relative to the diaphragm, for example, creates large asymmetries in the resistor bridge that contribute to temperature-dependent errors and nonlinearity in the transfer curve. Even the extreme positioning accuracy of microtechnology reaches its limit in this manufacturing operation.
Because ion implantation replaces only one of every million silicon atoms with a dopant atom, it integrates the resistors monolithically without altering the material's mechanical properties. In contrast to sensors with glued-on resistor stripes, the semiconductor sensor exhibits no mechanical defects from overload or aging.
Via aluminum conductors, the semiconductor resistors are joined together in a bridge configuration and attached to the bond pads for circuit interconnection. The resistors are placed on the diaphragm such that two experience mechanical tension in parallel and the other two are perpendicular to the direction of current flow. Thus, the two pairs exhibit resistance changes opposite to each other. These pairs are located diagonally in the bridge such that applied pressure produces a bridge imbalance (see Photo 2).
Photo 2. In this silicon pressure sensor, the piezoresistors are joined in a bridge configuration and attached to the bond pads for circuit interconnection. The two pairs are placed diagonally in the bridge such that applied pressure produces a bridge imbalance.
AssemblyAt one assembly stage, a wafer of ICs is bonded anodically to a wafer of Pyrex glass. (Anodic bonding is a pressure weld in which the two surfaces are pressed together while high current passes through the area of contact.) The bond creates a solid interconnection between the wafers in which mechanical tensions are absent. Because Pyrex and silicon have virtually the same thermal extension coefficients, this connection also avoids thermal tensions. Single chips are then cut from the compound wafer, bonded into a conventional package (often a metal can), and wire-bonded to the package electrical connectors (see Photo 3).
Photo 3. After anodic bonding to a Pyrex glass wafer, the individual chips are cut out of the wafer, bonded into a package such as the metal can shown here, and wire-bonded to the electrical connectors. Because Pyrex and silicon have virtually identical thermal extension coefficients, thermal tensions are eliminated by the bonding step.
The method of assembly has a substantial effect on the sensor's characteristic performance. These silicon sensors convert mechanical tension to an electrical signal and cannot distinguish between tensions due to the signal (pressure) and those caused by thermal changes or other effects. The sensor data therefore tend to have a thermal dependency. On the other hand, the fabrication techniques guarantee high precision and large volume at low cost and also allow the integration of compensation resistors and other sensors (temperature types, for instance) on the same piece of silicon.
Pressure sensors are characterized by parameters that depend on the target application. Comparisons are difficult because manufacturers are currently using different terminologies for the same sensor performance parameters. The user should therefore consider the condition of supply voltage and current corresponding to a particular data specification. The most relevant parameters are:
- α = Temperature coefficient of resistance
- Pnom = Nominal pressure range; the pressure range (in bars) for which the sensor complies with given data
- Pmax = Maximum pressure range; the maximum pressure the sensor can withstand without damage
- RB = Overall bridge resistance; the bridge resistance between the supply terminals, which changes with temperature
- αB = Temperature coefficient of bridge resistance; the change in bridge resistance as a function of temperature, in kelvin; useful to the signal-processing circuitry in measuring the sensor temperature
- VOS = Offset; the differential bridge voltage (in millivolts) at constant supply voltage, no pressure applied, and at the reference temperature
- αVOS = Temperature coefficient of offset; the change in offset as a function of the deviation from reference temperature, in millivolts/kelvin; assumes a linear relationship between the temperature and the offset change, which is true only for a limited range
- S = Sensitivity; describes the relationship between the sensor's rate of output change and the applied pressure at the reference temperature; often measured at the full-scale output (FSO)
- αS = Temperature coefficient of sensitivity; the change in sensitivity with temperature
- Linearity = The sensor's voltage/pressure relationship, expressed in terms of offset voltage and sensitivity, is not quite linear; deviations are <1%, but for precision applications they must be considered
VDIFF = VOS + TαVOS + P(S + TαS) (1)
Table 1 gives typical performance data for a series of pressure sensors developed at the Institute for Microelectronics and Information Technology in Germany. Though the diaphram thickness is a constant 15 microns, the devices offer a variation in diaphragm size that provides four different ranges of nominal pressure.
Table 1. Characteristic Data of Pressure Sensors Manufactured at the IMIT
欢迎分享,转载请注明来源:内存溢出
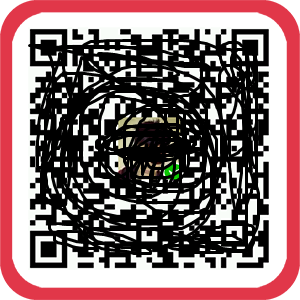
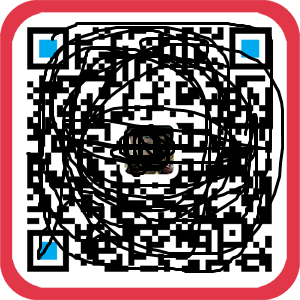
评论列表(0条)