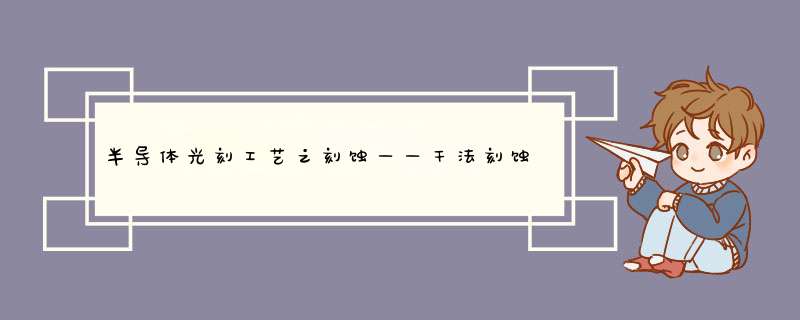
湿法
腐蚀的优点在于可以控制腐蚀液的化学成分,使得腐蚀液对特定薄膜材料的腐蚀速率远远大于其他材料的腐蚀速率,从而提高腐蚀的选择性。但是,由于湿法腐蚀的化学反应是各向同性的,因而位于光刻胶边缘下边的薄膜材料就不可避免的遭到腐蚀,这就使得湿法腐蚀无法满足ULSI工艺对加工精细线条的要求。所以相对于各向同性的湿法腐蚀,各向异性的干法
刻蚀就成为了当前集成电路技术中刻蚀工艺的主流。 一、干法刻蚀的原理 干法刻蚀是指利用
等离子体激活的化学反应或者是利用高能离子束轰击去除物质的方法。因为在刻蚀中并不使用溶液,所以称之为干法刻蚀。干法刻蚀因其原理不同可分为两种,一种是利用辉光放电产生的活性粒子与需要刻蚀的材料发生化学反应形成挥发性产物完成刻蚀,也称为等离子体刻蚀。第二种是通过高能离子轰击需要刻蚀的材料表面,使材料表面产生损伤并去除损伤的物理过程完成刻蚀,这种刻蚀是通过溅射过程完成的,也称为溅射刻蚀。上述两种方法的结合就产生了第三种刻蚀方法,称为反应离子刻蚀(简称RIE)。 在干法刻蚀中,纵向上的刻蚀速率远大于横向的刻蚀速率。这样,位于光刻胶边缘下边的材料,由于受到光刻胶的保护就不会被刻蚀。不过,在干法刻蚀的过程中,离子会对硅片上的光刻胶和无保护的薄膜同时进行轰击刻蚀,其刻蚀的选择性就比湿法刻蚀差(所谓的选择性是指刻蚀工艺对刻蚀薄膜和其他材料的刻蚀速率的比值,选择性越高,表示刻蚀主要是在需要刻蚀的材料上进行)。 在等离子体中存在有离子、电子和游离基(游离态的原子、分子或原子团)等,这些游离态的原子、分子或原子团等活性粒子,具有很强的化学活性,如果在这种等离子体中放入硅片,位于硅片表面上的薄膜材料原子就会与等离子体中的激发态游离基发生化学反应,生成挥发性的物质,从而使薄膜材料受到刻蚀,这就是等离子体刻蚀的原理和过程。因为等离子体刻蚀主要是通过化学反应完成的,所以具有比较好的选择性,但是各向异性就相对较差。 在溅射刻蚀过程中,等离子体的高能离子射到硅片表面上的薄膜表面时,通过碰撞,高能离子与被碰撞的原子之间就会发生能量和动量的转移,从而使被撞原子受到扰动。如果轰击离子传递给被撞原子的能量比原来的结合能(从几个eV到几十个eV)还要大,就会使被撞原子脱离原来的位置飞溅出来,产生溅射现象。例如,辉光放电中产生的氩离子,其能量高达500eV以上,这种高能离子束轰击硅片上的薄膜表面就会形成溅射刻蚀。溅射刻蚀的优点是各向异性刻蚀,而且效果很好,但是对刻蚀的选择性相对较差。 反应离子刻蚀是一种介于溅射刻蚀与等离子体刻蚀之间的干法刻蚀技术。在反应离子刻蚀中,同时利用了物理溅射和化学反应的刻蚀机制。反应离子刻蚀与溅射刻蚀的主要区别是,反应离子刻蚀使用的不是惰性气体,而是与等离子体刻蚀所使用的气体相同。由于在反应离子刻蚀中化学和物理作用都有助于实现刻蚀,因此就可以灵活的工作条件以求获得最佳的刻蚀效果。举例来说,如果某种气体的等离子体只与Si起化学反应,由于化学反应阻挡层SiO2的存在,就可以得到良好的Si/SiO2刻蚀速率比,从而保证刻蚀选择性的要求。反应离子刻蚀的缺点在于刻蚀重点难以检测。 综上所述,等离子体刻蚀和溅射刻蚀之间并没有明显的界限,一般来说,在刻蚀中物理作用和化学反应都可以发生。我们分析反应离子刻蚀、等离子体刻蚀和溅射刻蚀之间的关系可以看到:在反应离子刻蚀中,物理和化学作用都特别重要;在等离子体刻蚀中,物理效应很弱,主要是化学反应;而在溅射刻蚀中,几乎是纯物理作用。比较这三种刻蚀技术我们还可以发现,它们都是利用低压状态下(约0.01—133Pa)气体放电来形成等离子体作为干法刻蚀的基础,其区别是放电条件、使用气体的类型和所用反应系统的不同。刻蚀反应的模式取决于刻蚀系统的压力、温度、气流、功率和相关的可控参数。目前,在集成电路工艺过程中广泛使用的是反应离子技术。下面简要介绍采用干法刻蚀对集成电路制造中常用材料的刻蚀情况。 二、二氧化硅和硅的干法刻蚀 二氧化硅在集成电路工艺中的应用非常广泛,它可以作为隔离MOSFET的场氧化层,或者是MOSFET的栅氧化层,也可以作为金属间的介电材料,直至作为器件的最后保护层。因此,在集成电路工艺中对SiO2的刻蚀是最为频繁的。在ULSI工艺中对二氧化硅的刻蚀通常是在含有氟化碳的等离子体中进行。早期刻蚀使用的气体为四氟化碳(CF4),现在使用比较广泛的气体主要有CHF3、C2F4、SF4,其目的都是用来提供碳原子核和氟原子与SO2进行反应。以CF4为例,当CF4与高能量电子(约10eV以上)碰撞时,就会产生各种离子、原子团、原子和游离基。其中产生氟游离基和CF3分子的电离反应。氟游离基可以与SiO, 和Si 发生化学反应。反应将生成具挥发性的四氟化硅(SiF4)。 CF4+e——CF3 十F(游离基)+e SiO2+4F——SiF4(气)+02 Si+4F——SiF4(气) 在ULSI工艺中对SiO2 的干法刻蚀主要是用于刻蚀接触窗口,以MOSFET的接触窗口刻蚀为例。在MOSFET的上方覆盖有SiO2 层(通常是硼磷硅玻璃,简称BPSG), 为了实现金属层与 MOSFET的源/漏极之间的接触,需要刻蚀掉位于 MOSFET源/漏极上方的SiO2。为了使金属与 MOSFET源/漏极能够充分接触,源/漏极上方的SiQ2必须彻底清除。但是在使用CF4等离子体对SiO2进行刻蚀时,等离子体在刻蚀完 SiO2之后,会继续对硅进行刻蚀。因此,在刻蚀硅上的二氧化硅时,必须认真考虑刻蚀的选择性问题。 为了解决这一问题,在CF4 等离子体中通常加人一些附加的气体成份,这些附加的气体成份可以影响刻蚀速度、刻蚀的选择性、均匀性和刻蚀后图形边缘的剖面效果。 在使用CF4对硅和二氧化硅进行等离子刻蚀时,如果在CF4的等离子体中加人适量的氧气,氧气也同样被电离。其中,氧原子将与CF4反应生成CO和CO2 , 以及少量的COF2 ,另一方面,氟原子在与SiO2反应的同时,还与CF4原子团(x≤3)结合而消耗掉。在纯CF4等离子体中,由于存在使氟原子消耗的反应,造成氟原子的稳态浓度比较低,所以刻蚀的速度也比较慢。如果加入氧,则氧可与CFx原子团形成COF2 , CO和CO2, 造成CF, 原子团耗尽,从而减少了氟原子的消耗,进而使得CFx等离子体内的氟原子数对碳原子数的比例上升,其结果是氟原子的浓度增加,从而加快SiO2 的刻蚀速度。 对于CF, 刻蚀Si薄膜,也有相同的情况。在CF4刻蚀二氧化硅的过程中,氧的组分大约占20%时刻蚀的速度达到最大值。而使用CF4刻蚀硅,刻蚀速度最大时氧的组分大约占12% 。继续增加氧的组分,刻蚀速度将会下降,而且硅刻蚀速度的下降程度比刻蚀二氧化硅快。对于刻蚀 SiO2而言,氧的组分达到23%之前,刻蚀速度都是增加的,在达到氧组分临界值之后,由于氟原子浓度被氧冲淡,刻蚀速度开始下降。另一方面,由干于反应是在薄膜表面进行的,在刻蚀硅的情况下,氧原子倾向于吸附在Si的表面上,这样就部分地阻挡了氟原子加人反应。随着更多氧的吸附,对Si的刻蚀影响进一步增加。而在刻蚀二氧化硅时就不存在类似的效应。因为等效地看,SiO2的表面一开始就被氧原子所包围。因此,对硅的刻蚀速度最大时,其氧气的组分要小于刻蚀 SiO2的情况。 如果在CF4等离子体中加人氢,情况就会完全不同。在反应离子刻蚀二氧化硅的过程中,在相当低的气压下加大氢的组分,二氧化硅的刻蚀速度随氢的组分的增加而缓慢减小,这种情况可以持续到氢的组分大约占40%.而对于硅的刻蚀来说,刻蚀速度随氢组分的增加快速下降,当氢的组分大于40%时,对Si的刻蚀将停止。在CF4等离子体中加人氢对刻蚀的影响情况。 我们可以通过CF4等离子体刻蚀Si和SiO2的化学反应机制来解释这一现象。在刻蚀Si的过程中,氟原子与氢原子发生反应,从而使氢原子的浓度下降,这样等离子体中碳的含量升高,刻蚀反应就会被生成高分子聚合物的反应所代替,这就减小了对Si的刻蚀速度。另一方面,CFx(x≤3)原子团也可以与Si反应,生成挥发性的 SiF, 但是反应剩余的碳原子会吸附在Si的表面上,这些碳原子就会妨碍后续反应的进行。对于刻蚀SiO2的情况,氟原子也会与氢原子发生反应,氢原子的浓度下降也使SiO2的刻蚀速度减缓。面与刻蚀Si的情况不同的是,在CFx(x≤3)原子团与SiO2反应生成挥发性的SiF4的同时,CFx(X<3)原子团中的碳原子可以与二氧化硅中的氧原子结合,生成CO, CO2以及COF2气体,因此SiO2刻蚀速度的减缓程度要小于刻蚀Si的情况。在氢浓度超过40%以后,由于大量的氟原子与氢反应,CF4等离子体中的碳浓度开始上升,这也会在二氧化硅的表面形成高分个聚合物,从而使SiO2的刻蚀速度下降。 总的来看,在CF4等离子体中添加其他气体成份可影响等离子体内氟原子与碳原予的比例,简称F/C比。如果F/C比比较高(在CF4等离子体中添加氧气), 其影响倾向于加快刻蚀。反之,如果F/C比比较低(在CF4等离子体中添加氢气), 刻蚀过程倾向于形成高分子聚合物薄膜。 根据上述研究,可以通过在CF4等离子体中加人其他气体成份的方法,来解决选择性刻蚀 SiO2/Si的问题。如果CF4等离子体中O2的含量增加,刻蚀 Si 和刻蚀 SiO2的速度都加快,并且Si刻蚀速度的加快程度要大于刻蚀 SiO2的情况。因此,在CF4等离子体中加人O2将导致 SiO2/Si 刻蚀的选择性变差。在CF4等离子体中加人氢气对 SiO2的刻蚀影响不大,但是可以减小对Si的刻蚀速度。这说明在CF4等离子体中加人适量的氢气,将可以加强SiO2/Si刻蚀的选择性。 在当前集成电路工艺的干法刻蚀中,通常使用CHF3等离子体来进行SiO2的刻蚀。有时在刻蚀的过程中还要加人少量的氧气来提高刻蚀的速度。此外,SF6和NF3可以用来做为提供氟原子的气体。因为SF6和NF3中不含碳原子,所以不会在Si的表面形成高分子聚合物薄膜。 三、Si3N4的干法刻蚀 在ULSI工艺中,Si3N4的用途主要有两种:一种是在二氧化硅层上通过LPCVD 淀积Si3N4薄膜,然后经过光刻和干法刻蚀形成图形,做为接下来氧化或扩散的掩蔽层,但是并不成为器件的组成部分。这类Si3N4薄膜可以使用CF4, CF4(加O2, SF6和NF3)的等离子体刻蚀。另一种是通过 PECVD 淀积Si3N4做为器件保护层,这层 Si3N4 在经过光刻和干法刻蚀之后,氮化硅下面的金属化层露了出来,就形成了器件的压焊点,然后就可以进行测试和封装了。对于这种Si3N4薄膜,使用CF4-O2等离子体或其他含有F原子的气体等离子体进行刻蚀就可以满足要求。 实际上用于刻蚀SiO2的方法,都可以用来刻蚀 Si3N4.由于Si-N键的结合能介于Si-0键与 Si-Si键之间,所以氮化硅的刻蚀速度在刻蚀 SiO2和刻蚀Si之间。这样,如果对Si3N4/SiO, 的刻蚀中使用 CF4或是其他含氟原子的气体等离子体,对Si3N4/SiO2的刻蚀选择性将会比较差。如果使用 CHF3等离子体来进行刻蚀,对SiO2/Si的刻蚀选择性可以在10以上,而对Si3N4/Si的选择性则只有3~5左右,对 Si3N4/SiO2的选择性只有2~4左右。 刻蚀速率R是干法刻蚀的主要参数,刻蚀速率低,易于控制,但不适合实际生产要求。对于ULSI制造工艺,要有足够的刻蚀速率,且能重复、稳定的运用于生产中。这一节讨论几个影响刻蚀速率的主要因素。 四、离子能量和入射角 因为溅射刻蚀是利用物理溅射现象来完成的,所以,刻蚀速率由溅射率、离子束人射角和入射流密度决定,溅射率S定义为一个人射离子所能溅射出来的原子数。离子能量达到某一阈值能量以后(大约20 eV), 才能产生溅射,要想得到实用的溅射刻蚀速率,离子能量必须比阙值能量大得多(达几百eV以上)。在刻蚀工艺中离子的能量一般≤2keV, 在这 个能量范围内,大多数材料的溅射率随离子能量的增加单调上升,当离子能量达到一定程度之后,刻蚀速率随能量的增加是缓慢的。对于·ULSI所用的材料,Ar+离子能量为500eV 时,溅射率的典型值为0. 5~1. 5. 离子人射角表示离子射向衬底表面的角度(垂直于表面人射时,), 它是溅射率的敏感函数。当人射角大于零并增大时,衬底原子脱离表面飞出的几率增大,但是当人射角超过某一值时,在表面反射的离子增多,溅射率下降。人射角从零逐渐增加,S值也逐渐增大,在某一角度0-0max时,溅射率达到最大值,随后又逐渐减小,当0=90时,溅射率减小到零,即S=0. 在等离子体刻蚀和反应离子刻蚀中,溅射对刻蚀速率的贡献很小,更重要的是离子与材料表面之间的化学反应。但实验证明,由等离子体产生的中性粒子与固体表面之间的作用将加速反应,这种离子加速反应在许多干法蚀工艺中都起着重要作用。图8. 32是离子加速刻蚀的例子,图中分别给出Ar+和XeF2离子束射向硅表面的情况,每种离子束单独人射时,刻蚀速率都相当低。Ar+离子束是物理溅射刻蚀,XeF2解离为Xe 和两个F原子,然后,F原子自发地和硅反应形成挥发性氟化硅。当450 eV的Ar+离子束和XeF2气体同时人射时,刻蚀速率非常高,大约为两种离子束单独刻蚀速率总和的8倍。 图8. 33 表示的是离子加速反应的另一个例子,图中给出的是有Ar+存在时,CI2与硅的反应。与F原子不同,Cl2不能自发地刻蚀硅,当用450eV的Ar+离子束和Cl2同时射向表面时,硅被刻蚀,而且刻蚀速率比 Ar +溅射的刻蚀速率高得多。由图中可以看到,约轰击220秒时加人CI2气,刻蚀速率发生跃变,这是由于大量氯的存在所引起的。有几种可以解释离子加速反应的机理。① 离子轰击将在衬底表面产生损伤或缺陷,加速了化学反应过程;②离子轰击可直接离解反应剂分子(例如XeF2或Cl2)③离子轰击可以清除表面不挥发的残余物质。对这些机理及它们的相对重要性的研究仍旧是一个重要课题,并有所争论。 在上述的第一种情况中(XeF2十Si), 没有离子轰击时,离解的F原子可自发地刻蚀硅,但刻蚀速率低,在高能离子轰击下,提高了总刻蚀速率;在第二种情况下,没有高能离子轰击,(Cl2+Si)是不发生反应的。我们称前者为离子增强刻蚀;后一种情况称为离子感应刻蚀。 这两个例子说明,离子束刻蚀情况是与物过程有关的,并不是惰性气体离子的化学反应的贡献。在(XeF2十Si)和(Cl2+Si)的加速反应中,若离子能量为1keV时,Ar+, Ne+和He+离子的加速作用依次为Ar+>Ne+>He+。大量的研究结果表明,这些离子的加速作用与动量转移有关。但是,在CF4及其有关气体的等离子体刻蚀中,情况又不一样,这里离子本身就含有反应剂(例如CF3+)。在用XeF2刻蚀Si,并同时进行离子轰击的情况下,若用CF3+代替Ar+进行轰击,其刻蚀速率基本上不发生变化。因此,高能离子通过物理过程可以增强反应过程,与离子的化学反应无关。 对于反应离子刻蚀,等离子体中产生的主要是中性反应物,这些中性反应物先吸附于固体表面,再与表面原子反应,形成的反应物再解析成挥发性物质,整个反应可有等离子体中的高能离子诱发并加速。当然,高能离子提高反应速率的程度取决于所用的气体,材料和工艺参数的选取。 五、气体成份气体成份在等离子体刻蚀或反应离子到蚀中是影响刻蚀速率和选择性的关键因素,表8、1是VLSI制造中常用材料的一些代表性刻蚀气体。由表8.1可见,除了去除光削胶和刻蚀有机质之外,VLSI中主要使用卤素气体。选择气体的主要依据是,在等离子刻蚀温度(室温附近)下,它们是否能和剥蚀材料形成挥发性或准挥发性卤化物,由于含卤气体能相当容易地剂蚀VLSI所用的无机材料,而且工艺危害也很小,所以,卤化毒气体占有主要优势。 在反应刻蚀中,经常使用的是含多种成份的混合气体,这些混合气体由一种主要气体加入一种或几种添加剂组成,添加剂的作用是改善刻蚀速率、选择性、均匀性和刻蚀剖面。例如,在刻蚀Si和SiO2时,使用CF4为主的混合气体, 六、气体流速 气体流速决定反应剂的有效供给程度。反应剂的实际需要取决于有效反应物质产生与消耗之间的平衡过程,刻蚀剂损失的主要机制是漂移、扩散、复合以及附着和输运。 在一般工作条件中,气体流速射到蚀邃率R的影响不大,在极端情况下,可以观察到气体液邃的影响,例如,诙邃很小,刻蚀速率受反应剂供给量的限制1相反,当流邃很大时,输运成为反应剂损失的主要原因。是否发生输出损失取决于泵速、气体和反应器内的材料,在一般情况下,活性反应剂的寿命根短,流速的影响不必考虑}当活性剂的寿命较长(例如F原子)时,流速对刻蚀速率R产生影响,由图8.34可见,R-1是流速的线性函数,这与反应剂滞留时间与流速的关系一致,说明在所示的条件下,活性剂的寿命由输运损失决定。 七、温度在反应剥蚀中,M度对刻蚀速率的影响主要是通过化学反应j直率体现的。为获得均匀、重复的刻蚀速率,必须认真控制衬底温度,等离子体加热是衬底温度上升的主要原因;此外,刻蚀过程的放热效应也不可忽视。 八、压力、功率密度和频率 压力、功率密度和频率都是独立的工艺参数,但在实际中,它们各自对刻蚀工艺的影响是难以预计的。压力和频率较低,而功率密度较高,可以提高电子能量和人射离子的能量,增加功率也可提高等离子体中活性剂和离子的密度。因此,在离子加速反应刻蚀中,降低压力或频率,或增加功率密度,可以获得更好的各向异性刻蚀。 一般刻蚀速率单调地随功率而增加。由于外加功率几乎都要转变为热量,因此,在功率密度板高时,样品温度升高,需要考虑衬底散热,否则,会造成有害的影响。 系统压力对到蚀速率的影响,随刻蚀材料及气体的不同而有明显的差异。随着系统压力増加,刻蚀速率增大,选择合适的刻蚀条件可以获得最大的刻恤速率。 频率主要是通过离子能量面影响到蚀速率。放电的工作电压障频率的降低而增加,因而离子的轰击能量在低频下将比高频下的高,又因为刻蚀速率与您轰击能量成正比,所以,在低频下能获得比较高的划蚀速率。 九、负载效应 在反应刻蚀的过程中,刻蚀的速率往往隲刻蚀面积的增大而减小,这种现象称为负载效应。当反应剂与剥蚀材料的反应迅速时,容易产生负戦效应。如果刻蚀是反应剂的主要损失机制,则刻蚀材料的表面积越大,反应剂的消耗速率就越快。活性物质的产生率由工艺参数(例如压力、功率、频率等)决定,与到蚀材料的多少无关、这样,反应刑的平衡浓度可由产生率和损失率之差决定,在反应离子刻蚀的过程中,刻蚀速率只与被刻蚀的面积成反比,刻蚀的速率R随被刻蚀的面积的増大而减小。这说明在一次刻蚀的过程中,需要刻蚀的硅片数目越多,由于反应原子和原子团的消耗,整体的刻蚀速率就越慢。若等离子体中反应刑的寿命很短,负载效应很小就可以忽略,反应剂的损失机构主要由刻蚀消耗所决定。 在集成电路工艺中,负载效应的出现,将影响图形尺寸的精确控制,因为,随着刻蚀到达终点,被腐材料的表面积迅速减小,此时的刻蚀速率就会比正常划蚀速率高得多,不但进行过刻蚀,而且也加速了倒向刻蚀,给条宽的控制造成困难。 从某种意义上说,负载效应是一种宏观过程,反应室中某个硅片的存在将影响另一硅片的刻蚀速率,这就意味着等离子体中反应剂的输运过程非常迅速,以致等离子体中的反应剂并不存在多大的浓度梯度。当然,被多打虫图形的尺寸和密度不同,也会影响刻蚀速率,这可能是由于反应速率不同,引起反应剂的局部浓度梯度而造成的。在湿法腐蚀的过程中,通过使用特定的熔液与需要腐蚀的薄膜材料进行化学反应,进而除去没有被光刻胶覆盖区域的薄膜。 湿法腐蚀的优点是工艺简单,但是在湿法腐蚀中所进行的化学反应没有特定方向,所以会形成各向同性的腐蚀效果。各向同性是湿法腐蚀固有的特点,也可以说是湿法腐蚀的缺点。湿法腐蚀通常还会使位于光刻胶边缘下边的薄膜也被腐蚀,这也会使腐蚀后的线条宽度难以控制,选择合适的腐蚀速度,可以减小对光刻胶边缘下边薄膜的腐蚀。 在进行湿法腐蚀的过程中,熔液里的反应剂与被腐蚀薄膜的表面分子发生化学反应,生成各种反应产物。这些反应产物应该是气体,或者是能溶于腐蚀液中的物质。这样,这些反应产物就不会再沉积到被腐蚀的薄膜上。控制湿法腐蚀的主要参数包括:腐蚀溶液的浓度、腐蚀的时间、反应温度以及溶液的搅拌方式等。由于湿法腐蚀是通过化学反应实现的,所以腐蚀液的浓度越高,或者反应温度越高,薄膜被腐蚀的速率也就越快。此外,湿法腐蚀跌反应通常会伴有放热和放气。反应放热会造成局部反应温度的升高,使反应速度加快;反应速率加快又会加剧反应放热,使腐蚀反应处于不受控制的恶性循环中,其结果将导致腐蚀的图形不能满足要求。反应放气产生的气泡会隔绝局部的薄膜与腐蚀的接触,造成局部的反应停止,形成局部的缺陷。因此,在湿法腐蚀中需要进行搅拌。此外,适当的搅拌(例如使用超声波震荡),还可以在一定程度上减轻对光刻胶下方薄膜的腐蚀。 目前常用的湿法腐蚀的材料包括:Si,SiO2和Si2N4等,下面我们将对此进行简要讨论。 一、Si的湿法腐蚀 在湿法腐蚀Si的各种方法中,大多数都是采用强氧化剂对Si进行氧化,然后利用HF酸与SiO2反应来去除SiO2,从而达到对硅的腐蚀目的。最常用的腐蚀溶剂是硝酸与氢氟酸和水(或醋酸)的混合液,化学反应方程式为 Si+HNO3+6HF——H2SiF4+HNO2+H2O+H2 其中,反应生成的H2SiF4可溶于水。在腐蚀液中,水是作为稀释剂,但最好用醋酸(CH3COOH),因为醋酸可以抑制硝酸的分解,从而使硝酸的浓度维持在较高的水平。对于HF-HNO3混合的腐蚀液,当HF的浓度高而HNO3的浓度低时,Si膜腐蚀的速率由HNO3浓度决定(即Si的腐蚀速率基本上与HF浓度无关),因为这时有足量的HF去溶解反应中生成的SiO2.当HF的浓度低而HNO3浓度高时,Si腐蚀的速率取决于HF的浓度(即取决于HF溶解反应生成的SiO2的能力)。 对Si的湿法腐蚀还可以用KOH的水溶液与异丙醇(IPA)相混合来进行。对于金刚石或闪锌矿结构,(111)面的原子比(100)面排的更密,因而(111)面的腐蚀速度应该比(100)面的腐蚀速率小。 采用SiO2层作为掩膜对(100)晶向的硅表面进行腐蚀,可以得到V形的沟槽结构。如果SiO2上的图形窗口足够大,或者腐蚀的时间比较短,可以形成U形的沟槽。如果被腐蚀的是(110)晶向的硅片,则会形成基本为直壁的沟槽,沟槽的侧壁为(111)面。这样就可以利用腐蚀速率对晶体取向的依赖关系制得尺寸为亚微米的器件结构。不过,这种湿法腐蚀的方法大多采用在微机械元件的制造上,在传统的集成电路工艺中并不多见。 二、SiO2的湿法腐蚀 SiO2的湿法腐蚀可以使用氢氟酸(HF)作为腐蚀剂,其反应方程式为: SiO2+6HF——SiF4+2H2O+H2 在上述的反应过程中,HF不断被消耗,因此反应速率随时间的增加而降低。为了避免这种现象的发生,通常在腐蚀液中加入一定的氟化氨作为缓冲剂(形成的腐蚀液称为BHF)。氟化氨分解反应产生HF,从而维持HF的浓度。NH4F分解反应方程式为 NH4F——NH3+HF 分解反应产生的NH3以气态被排除掉。 在集成电路工艺中,除了需要对热氧化和CVD等方式得到的SiO2进行腐蚀外,还需要对磷硅玻璃(简称PSG)和硼磷硅玻璃(简称BPSG)等进行腐蚀。因为这些二氧化硅层的组成成分并不完全相同,所以HF对这些SiO2的腐蚀速率也就不完全一样。基本上以热氧化方式生成的二氧化硅层的腐蚀速率最慢。 三、Si3N4的湿法腐蚀 Si3N4也是一种常用湿法腐蚀的材料。Si3N4可以使用加热的磷酸(130-150度的H3PO4)来进行腐蚀。磷酸对Si3N4的腐蚀速率通常大于对SiO2的腐蚀速率。
前些天,我国本土半导体设备传来好消息,中微半导体设备(上海)有限公司自主研制的5nm等离子体刻蚀机经台积电验证,性能优良,将用于全球首条5nm制程生产线。刻蚀机是芯片制造的关键装备之一,中微突破关键核心技术,让“中国制造”跻身刻蚀机国际第一梯队。
近年来,我国大陆半导体设备企业一直在努力追赶国际先进脚步。在多种设备领域有一定突破,除了上述中微半导体的5nm等离子体刻蚀机之外,有越来越多的产品可应用于14nm、7nm制程。
但是,国内设备与国外先进设备相比仍有较大差距,主要表现在两方面:一是有一定竞争力的产品在领先制程上的差距;二是部分产品完全没有竞争能力或尚未布局,比如国内光刻机落后许多代际,仅能达到90nm的光刻要求,国内探针台也处于研发阶段,尚未实现销售收入。
那么,在国家的扶持下,经过这么多年的发展,我国本土半导体设备各个细分领域的发展情况如何呢?相关企业都有哪些?发展到了什么程度呢?下面就来梳理一下。
北方华创
北方华创由七星电子和北方微电子战略重组而成。七星甴子主营清洗机、氧化炉、 气体质量控制器(MFC)等半导体装备及精密甴子元器件等业务,此外七星甴子还是国内真空设备、 新能源锂甴装备重要供应商。北方微甴子主营刻蚀设备(Etch)、物理气相沉积设备(PVD)、化学气相沉积设备(CVD)三类设备。
2010 年 3 月,七星甴子在深交所上市。 2016 年 8 月,七星甴子与北方微甴子实现战略重组,成为中国规模最大、产品体系最丰富、涉及领域最广的高端半导体工艺设备供应商,开成功引迚国家集成甴路产业基金(大基金)等战略投资者,实现了产业与资本的融合。 公司实际控制人是北京甴控,隶属于国资委。
2017 年 2 月,七星甴子正式更名为北方华创 科技 集团股仹有限公司,完成了内部整合,推出全新品牉“北方华创”,开形成了半导体装备、真空装备、新能源锂甴装备和高精密甴子元器件四大业务板块加集团总部的“4+1”经营管理模式。
北方华创的半导体装备亊业群主要包括刻蚀机、 PVD、 CVD、氧化炉、扩散炉、清洗机及质量流量控制器(MFC)等 7 大类半导体设备及零部件,面向集成甴路、先进封装等 8 个应用领域,涵盖了半导体生产前段工艺制程中的除光刻机外的大部分兲键装备。 客户包括中芯国际、华力微甴子、长江存储等国内一线半导体制造企业,以及长甴 科技 、 晶斱 科技 、华天 科技 等半导体封装厂商。
重组之后,北方华创业绩快速增长。2017 年实现营业收入 22.23 亿元,同比增长37.01%,归母净利润 1.26 亿元,同比增长 35.21%。 根据公司 2018 年半年报业绩快报,2018 年上半年公司实现营业收入13.95 亿元,同比增长 33.44%, 归母净利润 1.19 亿元,同比增长 125.44%。 随着下游晶圆厂投资加速, 公司半导体设备等觃模持续扩张。
长川 科技
长川 科技 是国内集成电路封装测试、晶圆制造及芯片设计环节测试设备主要供应商。 半导体测试设备主要包括分选机、 测试机和探针台三大类。自2008年4月成立以来,该公司率先实现了半导体测试设备(分选机和测试机) 的国产化, 并获得国内外众多一流集成电路企业的使用和认可。
该公司于 2012 年 2 月承担并完成国家“十二五”规划重大专项“极大规模集成电路制造装备及成套工艺”中的高端封装设备与材料应用工程项目,并于 2015 年 3 月获得国家集成电路产业基金投资。
该公司的测试机和分选机在核心性能指标上已达到国内领先、接近国外先进水平,同时售价低于国外同类型号产品,具备较高的性价比优势。 公司产品已进入国内主流封测企业, 如天水华天、 长电 科技 、 杭州士兰微、 通富微电等。 2017 年,该公司对外积极开拓市场, 设立台湾办事处,拓展台湾市场。
2013~2017年,长川 科技 营收实现了由 4,341 万元到 1.80 亿元的跨越,复合增速达39.75%。 2017 年,归属母公司净利润由992万元增长至 5,025 万元, 复合增速达31.48%。
中微半导体
中微半导体成立于 2004 年,是一家微加工高端设备公司, 经营范围包括研发薄膜制造设备和等离子体刻蚀设备、大面积显示屏设备等。该公司管理层技术底蕴深厚,大多有任职于应用材料、LAM和英特尔等全球半导体一流企业的经验。
中微半导体先后承担并圆满完成 65-45 纳米、 32-22 纳米、22-14 纳米等三项等离子介质刻蚀设备产品研制和产业化。 公司自主研发的等离子体刻蚀设备 Primo D-RIE 可用于加工 64/45/28 纳米氧化硅、氮化硅等电介质材料,介质刻蚀设备 Primo AD-RIE 可用于 22nm 及以下芯片加工,均已进入国内先进产线。中微半导体的介质刻蚀机已经完成了5nm 的生产。
晶盛机电
晶盛机电是一家专业从事半导体、光伏设备研发及制造的高新技术企业,是国内技术领先的晶体硅生长设备供应商。该公司专注于拥有自主品牌的晶体硅生长设备及其控制系统的研发、制造和销售,先后开发出拥有完全自主知识产权的直拉式全自动晶体生长炉、铸锭多晶炉产品。
该公司立足于“提高光电转化效率、降低发电成本”的光伏技术路线,实现了硅晶体生长“全自动、高性能、高效率、低能耗”国内领先、国际先进的技术优势。全自动单晶炉系列产品和 JSH800 型气致冷多晶炉产品分别被四部委评为国家重点新产品。同时公司积极向光伏产业链装备进行延伸,2015 年成功开发并销售了新一代单晶棒切磨复合一体机、单晶硅棒截断机、多晶硅块研磨一体机、多晶硅块截断机等多种智能化装备,并布局高效光伏电池装备和组件装备的研发。
该公司的晶体生长设备特别是单晶硅生长炉销售形势较好,主要是单晶光伏的技术路线获得认可,随着下游厂商的扩产,单晶的渗透率也逐步提升,带来对单晶硅生长炉的需求增加,该类产品收入已经占营业收入的 81%。
该公司主营业务伴随国内光伏产业的上升发展,给主营业务收入和利润带来显着增长,近两年的增长率均在 80%以上,另外,其毛利率水平和净利率水平也基本维持稳定。
上海微电子
上海微电子装备有限公司成立于2002年,主要致力于大规模工业生产的投影光刻机研发、生产、销售与服务,该公司产品可广泛应用于IC制造与先进封装、MEMS、TSV/3D、TFT-OLED等制造领域。
该公司主要产品包括:
600扫描光刻机系列—前道IC制造
基于先进的扫描光刻机平台技术,提供覆盖前道IC制造90nm节点以上大规模生产所需,包含90nm、130nm和280nm等不同分辨率节点要求的ArF、KrF及i-line步进扫描投影光刻机。该系列光刻机可兼容200mm和300mm硅片。
500步进光刻机系列—后道IC、MEMS制造
基于先进的步进光刻机平台技术,提供覆盖后道IC封装、MEMS/NEMS制造的步进投影光刻机。该系列光刻机采用高功率汞灯的ghi线作为曝光光源,其先进的逐场调焦调平技术对薄胶和厚胶工艺,以及TSV-3D结构等具有良好的自动适应性,并通过采用具有专利的图像智能识别技术,无需专门设计特殊对准标记。该系列设备具有高分辨率、高套刻精度和高生产率等一系列优点,可满足用户对设备高性能、高可靠性、低使用成本(COO)的生产需求。
200光刻机系列—AM-OLED显示屏制造
200系列投影光刻机综合采用先进的步进光刻机平台技术和扫描光刻机平台技术,专用于新一代AM-OLED显示屏的TFT电路制造。该系列光刻机不仅可用于基板尺寸为200mm × 200mm的工艺研发线,也可用于基板尺寸为G2.5(370mm × 470mm)和G4.5(730mm × 920mm)的AM-OLED显示屏量产线。
硅片边缘曝光机系列——芯片级封装工艺应用
SMEE开发的硅片边缘曝光机提供了满足芯片级封装工艺中对硅片边缘进行去胶处理的能力,设备可按照客户要求配置边缘曝光宽度、硅片物料接口形式、曝光工位等不同形式。设备同时兼容150mm、200mm和300mm等三种不同规格的硅片,边缘曝光精度可到达0.1mm。设备配置了高功率光源,具有较高的硅片面照度,提高了设备产率。
至纯 科技
至纯 科技 成立于 2000 年, 主要为电子、生物医药及食品饮料等行业的先进制造业企业提供高纯工艺系统的整体解决方案, 产品为高纯工艺设备和以设备组成的高纯工艺系统,覆盖设计、加工制造、安装以及配套工程、检测、厂务托管、标定和维护保养等增值服务。
该公司在 2016年前产品约一半收入来自医药类行业,光伏、 LED 行业及半导体行业收入占比较小。 2016年以来,公司抓住半导体产业的发展机遇,逐步扩大其产品在半导体领域的销售占比, 2016和 2017 年来自半导体领域收入占公司营业收入比重分别为 50%和 57%,占据公司营业收入半壁江山。主攻半导体清洗设备。
该公司于 2015 年开始启动湿法工艺装备研发, 2016 年成立院士工作站, 2017 年成立独立的半导体湿法事业部至微半导体,目前已经形成了 UltronB200 和 Ultron B300 的槽式湿法清洗设备和 Ultron S200 和 Ultron S300 的单片式湿法清洗设备产品系列, 并取得 6 台的批量订单。
精测电子
武汉精测电子技术股份有限公司创立于 2006 年 4 月,并于 2016 年 11 月在创业板上市。公司主要从事平板显示检测系统的研发、生产与销售,在国内平板显示测试领域处于绝对领先地位, 主营产品包括:模组检测系统、面板检测系统、OLED 检测系统、AOI光学检测系统和平板显示自动化设备。近几年来,该公司积极对外投资,设立多家子公司,业务规模迅速扩张,进一步完善了产业布局。
该公司成立初期主要专注于基于电讯技术的信号检测,是国内较早开发出适用于液晶模组生产线的 3D 检测、基于 DP 接口的液晶模组生产线的检测和液晶模组生产线的 Wi-Fi 全无线检测产品的企业,目前该公司的 Module 制程检测系统的产品技术已处于行业领先水平。
2014 年,精测电子积极研发 AOI 光学检测系统和平板显示自动化设备,引进了宏濑光电和台湾光达关于 AOI 光学检测系统和平板显示自动化设备相关的专利等知识产权,使其在 Array制程和 Cell 制程的检测形成自有技术,初步形成了“光、机、电”技术一体化的优势。
精测电子2018年上半年财务报告显示,该公司收入主要来自 AOI 光学检测系统业务,占比 45.49%,毛利占比 41.94%;其次是模组检测系统业务,收入占比 23.33%,毛利占比 27.68%; OLED 检测系统和平面显示自动化设备收入占比分别为 14.29%和12.30%,毛利占比为 14.26%和 10.28%。
电子 科技 集团45所
中国电子 科技 集团公司第45研究所创立于1958年,2010年9月,中央机构编制委员会办公室批准45所第一名称更改为“北京半导体专用设备研究所”,第二名称仍保持“中国电子 科技 集团公司第四十五研究所”不变。
45所是国内专门从事军工电子元器件关键工艺设备技术、设备整机系统以及设备应用工艺研究开发和生产制造的国家重点军工科研生产单位。
45所以光学细微加工和精密机械与系统自动化为专业方向,以机器视觉技术、运动控制技术、精密运动工作台与物料传输系统技术、精密零部件设计优化与高效制造技术、设备应用工艺研究与物化技术、整机系统集成技术等六大共性关键技术为支撑,围绕集成电路制造设备、半导体照明器件制造设备、光伏电池制造设备、光电组件制造和系统集成与服务等五个重点技术领域,开发出了电子材料加工设备、芯片制造设备、光/声/电检测设备、化学处理设备、先进封装设备、电子图形印刷设备、晶体元器件和光伏电池等八大类工艺设备和产品,服务于集成电路、光电元器件与组件、半导体照明和太阳能光伏电池四大行业.
上海睿励
睿励科学仪器(上海)有限公司是于2005年创建的合资公司,致力于研发、生产和销售具有自主知识产权的集成电路生产制造工艺装备产业中的工艺检测设备。主要生产用于65/28/14nm制程工艺控制的膜厚测量设备。
沈阳芯源
沈阳芯源微电子设备有限公司成立于2002年,由中科院沈阳自动化研究所引进国外先进技术投资创建。
芯源公司自主开发的单片匀胶机、显影机、喷胶机、去胶机、清洗机、湿法刻蚀机等设备广泛应用于半导体、先进封装、MEMS、LED等领域。
1.LED领域匀胶显影机:应用于LED芯片制造、PSS(图形化衬底)、MEMS、HCPV(高聚光型太阳能电池)、Waveguide(光波导)工艺的匀胶显影等工艺制程。
2.高端封装全自动涂胶显影机:广泛应用于先进封装BGA、Flip-Chip、WSP、CSP制程的高黏度PR、PI、Epoxy的涂敷、显影工艺制程。
3.高端封装全自动喷雾式涂胶机: 广泛应用于TSV、MEMS、WLP等工艺制程。
4.单片湿法刻蚀机/去胶机/清洗机:广泛应用于先进封装BGA、Flip-Chip、WSP、CSP制程的刻蚀、去胶、清洗工艺制程。
5.前道堆叠式全自动涂胶显影机:应用于90nm光刻工艺、BARC涂覆、SOC、SOD、SOG等工艺制程。
盛美半导体
盛美半导体(ACM Research)是国内半导体清洗设备主要供应商,于1998年在美国硅谷成立,主要研发电抛光技术,2006 年成立上海子公司,专注于半导体清洗设备。2017年11月4日公司在美国纳斯达克上市。2017年公司营业收入3650万美元,同比增长33.2%,其中90%以上的营业收入来自于半导体清洗设备。2017 年研发投入占营业收入比例为14.1%。
由于声波清洗可能会造成晶片损伤,行业公司大多转向研发其他技术,盛美半导体另辟蹊径研发出空间交变相移兆声波清洗(SAPS)和时序能激气泡震荡兆声波清洗(TEBO)两项专利技术,可以实现无伤清洗。公司的清洗设备目前已经进入 SK 海力士、长江存储和上海华力等先进产线。
天津华海清科
天津华海清科机电 科技 有限公司成立于2013年,是天津市政府与清华大学践行“京津冀一体化”国家战略,为推动我国化学机械抛光(CMP)技术和设备产业化成立的高 科技 企业。
华海清科主要从事CMP设备和工艺及配套耗材的研发、生产、销售与服务,核心团队成员来自清华大学摩擦学国家重点实验室及业内专业人才,产品可广泛应用于极大规模集成电路制造、封装、微机电系统制造、晶圆平坦化、基片制造等领域。
中电科装备
中电科电子装备集团有限公司成立于2013年,是在中国电子 科技 集团公司2所、45所、48所基础上组建成立的二级成员单位,属中国电子 科技 集团公司独资公司,注册资金21亿元,该公司是我国以集成电路制造装备、新型平板显示装备、光伏新能源装备以及太阳能光伏产业为主的科研生产骨干单位,具备集成电路局部成套和系统集成能力以及光伏太阳能产业链整线交钥匙能力。
多年来,利用自身雄厚的科研技术和人才优势,形成了以光刻机、平坦化装备(CMP)、离子注入机、电化学沉积设备(ECD)等为代表的微电子工艺设备研究开发与生产制造体系,涵盖材料加工、芯片制造、先进封装和测试检测等多个领域;通过了ISO9001、GJB9001A、UL、CE、TüV、NRE等质量管理体系与国际认证。
沈阳拓荆
沈阳拓荆 科技 有限公司成立于2010年4月,是由海外专家团队和中科院所属企业共同发起成立的国家高新技术企业。拓荆公司致力于研究和生产薄膜设备,两次承担国家 科技 重大专项。2016年、2017年连续两年获评“中国半导体设备五强企业”。
该公司拥有12英寸PECVD(等离子体化学气相沉积设备)、ALD(原子层薄膜沉积设备)、3D NAND PECVD(三维结构闪存专用PECVD设备)三个完整系列产品,技术指标达到国际先进水平。产品广泛应用于集成电路前道和后道、TSV封装、光波导、LED、3D-NAND闪存、OLED显示等高端技术领域。
华海清科
天津华海清科机电 科技 有限公司成立于2013年,是天津市政府与清华大学践行“京津冀一体化”国家战略,为推动我国化学机械抛光(CMP)技术和设备产业化成立的高 科技 企业。
华海清科主要从事CMP设备和工艺及配套耗材的研发、生产、销售与服务,核心团队成员来自清华大学摩擦学国家重点实验室及业内专业人才,产品可广泛应用于极大规模集成电路制造、封装、微机电系统制造、晶圆平坦化、基片制造等领域。
以上就是我国大陆地区的主要半导体设备生产企业。
随着我国半导体产业的快速发展,对半导体设备的需求量越来越大,而本土半导体设备企业面临着供给与需求错配的情况。一方面,国内的半导体设备需求随着下游产线的扩张而迅速增加,大陆的半导体设备需求占全球半导体设备需求的比重较高;但另一方面,本土的设备供给存在着水平较为落后,国产化率不高的情况。
针对这一情形,在国家的大力支持下,国内设备企业需要积极布局,以在各细分设备领域实现突破。
评论列表(0条)