半导体制造中的大部分材料是多晶材料,比如互连线和接触孔。XRD能够将多晶材料的一系列特性量化。这其中最重要的特性包括多晶相(镍单硅化物,镍二硅化物),平均晶粒大小,晶体织构,残余应力。直到现在,多晶XRD并没有应用于量测技术,因为获得衍射图形需要很长的时间,得到数据的物理意义也比较复杂。然而,随着二维场探测仪和先进数据冗余处理算法的发展,XRD量测设备已经成为可能。
设备
第一代应用于多晶材料的XRD量测设备由HyperNex Inc和IBM共同研发,并安装在IBM位于纽约East Fishkill的半导体研发生产工厂。该设备的硬件设计极具针对性,它包括固定的放射源和探测器,可以在xy水平方向移动,在方位角方向旋转的水平采样载物台。水平载物台需要与硅片的传送机械臂兼容,而xy传送载物台允许全硅片映射,它的重要性在随后的章节中会变得显而易见。X射线束使用可变的缝状源,从而使得光束采样可以覆盖从50um到1mm的范围。宽光束用来扫描无图形的硅片,窄光束用来获得有图形硅片上独立结构的衍射谱线。描述独立结构特性的需求决定了系统必须具备视频显微镜和图形识别软件。为了满足高速产出的需要,二维场探测仪被用来收集衍射谱线。图1说明了一幅探测仪收集到的衍射谱线。将场探测仪收集的图形组合起来便是传统的衍射图形(图2),它可以用作相鉴定和多相薄膜中相数的量化,图形中根据环强度的变化可以获得该材料晶体织构的信息,环的宽度决定了相关晶粒的大小。
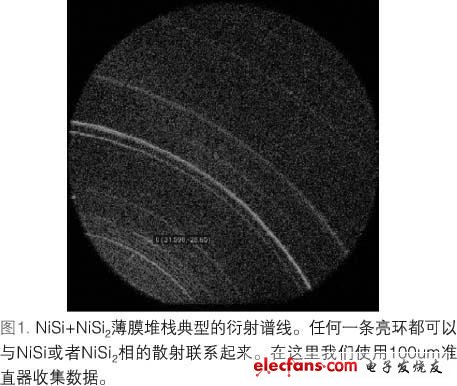
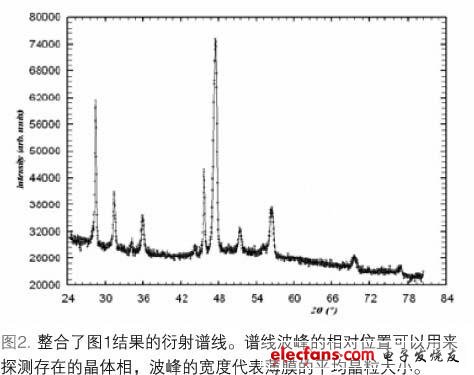
因为受硅片产出量的限制,在这些设备上进行残留应力的测量并不现实。剩下的相位,晶粒大小和织构都是可测量的参数。我们所面临的挑战是如何将图1和图2所示的庞大图形数据量精简为几个相关参数,而这些参数可以加入统计过程控制(SPC)图表。在这些参数当中,晶粒尺寸是最容易获得的,对于给定的相而言,衍射峰之间的宽度与材料晶粒的平均尺寸成反比。另外两个参数的测量则面临着较大的挑战,因为一般而言,它们依赖于精通X射线衍射理论和应用的个人对图形数据进行个别的诠释。
相分析要求事先了解感兴趣的相。一种自动化的峰拟合算法用来获得曲线中每一个峰的位置和强度值。将实验峰值的位置与感兴趣相的谱线作对比,来确定该相是否存在。另外,曲线中不能被匹配的峰意味着更多的相存在。例如在图2中,如果取样程式认为在测量的硅片上只存在镍单硅化物,尽管事实上相的鉴定需要手工完成,但多余的峰(来自于NiSi2)仍然会被软件标记。为了测量不同相的比例,一种针对多相系统的应用遵循了这样的原理,即一个独立相衍射峰的强度(一级近似)与薄膜中对应相的数量成比例。
晶体织构的计算可以自动完成,使用者并不需要输入任何信息,计算结果会发送到主机软件,这一点和标准的量测设备很相像。通过将X射线的强度转换为极图空间里的极密度,给定相原始的二维X射线图形可以精简为晶体织构强度的量化值。探测仪由于可以覆盖较大的范围,使得我们可以为每一个相收集等同于几个局部极图的数据。从这些极图可以计算出方向分布函数并作为工具量化织构。读者可以从参考文献[4]中得到更多详细信息。
应用
根据配置的不同,一台线上XRD设备可以作为完全的量测设备,或者作为日常监测、问题诊断、工艺研发的多功能设备。因为IBM工厂身兼生产与研发两种角色,XRD设备在设计时就已经考虑到其在两种角色之间如何切换的问题。日常监测功能提出了与问题诊断和工艺开发不同的要求。在线上的日常监测中,只需要建立一个单一程式。设备载入硅片并将数据自动加入一系列控制图表之中,这一过程不需要 *** 作者介入。薄膜堆栈中的任一种材料只有1-2个不同的结构参数被监测。相反,对于问题诊断和工艺研发,虽然只有一至两盒硅片参与量测,但需要精通X射线衍射的专家查看得到的所有数据。
表1总结出半导体生产中可以通过X射线衍射量测的多晶材料。几种有代表性的应用技术在下面详细列出。
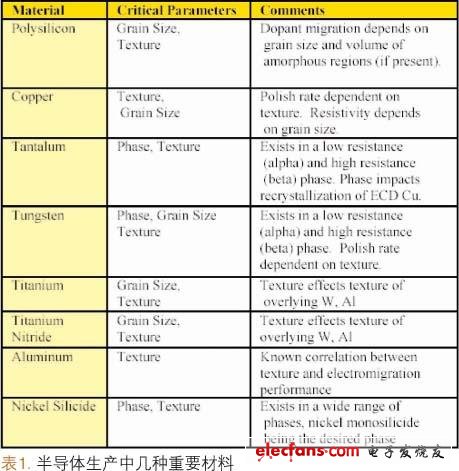
欢迎分享,转载请注明来源:内存溢出
评论列表(0条)