挑战:连杆是发动机的关键部件之一,其可靠性对整机寿命具有至关重要的作用。为了研究发动机连杆在拉压载荷下的疲劳特性,所研制的发动机连杆试验台基于美国NI公司的LabVIEW开发环境和CompactRIO嵌入式控制器,采用液压伺服的加载方式对连杆进行拉压加载。如何根据发动机及连杆的参数确定加载载荷和加载频率?如何控制液压系统按照设定的加载载荷和频率进行加载?如何实时监测试验状态,判断连杆发生疲劳破坏?如何采集、存储、分析相关数据得出相应的试验结果?这是整套试验系统的关键所在。
使用的产品:
LabVIEW 2009
LabVIEW RT 9.0
LabVIEW FPGA 9.0
LabVIEW PID Control Toolkit 9.0.0
CompactRIO-9014可重新配置嵌入式机箱
CompactRIO-9014嵌入式控制器
CompactRIO-9237应变信号采集模块
CompactRIO-9205电压信号采集模块
CompactRIO-9263电压信号输出模块
CompactRIO-9401 DIO模块
CompactRIO-9485 SSR模块
正文:
引言
强度、刚度和疲劳寿命是衡量工程机械机构和零件可靠性的主要参数,疲劳破坏是机械机构和零件失效的主要原因之一(据统计,连杆60%到90%的破坏都是疲劳破坏),而引起疲劳破坏的主要原因是动态交变载荷。
连杆是往复活塞式内燃机的核心部件,也是内燃机中承受较大交变载荷的主要部件之一,其可靠性直接影响内燃机运行的安全。
目前开展连杆疲劳可靠性研究的主要手段包括仿真计算、实机试验和模拟疲劳试验。
仿真计算方便、快捷、成本低,针对连杆的仿真计算很多,但只能对疲劳可靠性进行趋势性的分析和验证,并且边界条件不确定;实机试验可以反映连杆的真实工况,但试验周期长、成本较高,并且不能进行强化试验;模拟疲劳试验可以用较短的周期较高的效率来进行试验,并可以对疲劳试验进行强化,更全面的检验连杆的疲劳特性。
目前,国内多为国外引进设备,尚未有自主研发的连杆拉压模拟疲劳试验台。因此,研制发动机连杆拉压模拟疲劳试验台具有较大的意义。在试验台的开发上,美国NI公司的LabVIEW开发环境和CompactRIO嵌入式控制器及其配套板卡为我们提供强有力的工具。
试验系统总体介绍
2.1连杆受力情况
如图1所示,在发动机运行过程中,连杆的运动状态比较复杂,小头作往复运动,大头作旋转运动,杆身作平面运动。同时,连杆的受力情况也十分复杂,连杆在实际工况中的受力可分为两部分:一部分是工作中产生的气体爆发压力和活塞组件的往复惯性力;另一部分是连杆运动时本身产生的惯性力,包括往复惯性力,摆动离心力和横向弯矩(横向弯矩相对较小,并且其极值不与其他力一同出现,因此忽略不计)。
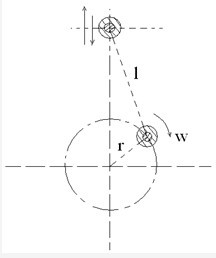
图1:发动机连杆机构示意图
在以上各力的作用下每一个截面上都会有弯矩、剪力和法向力。但弯矩和剪力与法向力相比都不大,连杆主要承受的是交变的拉压载荷。
欢迎分享,转载请注明来源:内存溢出
评论列表(0条)