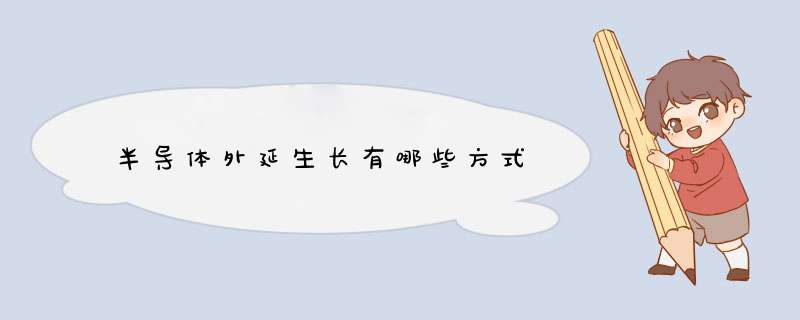
外延(Epitaxy, 简称Epi)
工艺是指在单晶衬底上生长一层跟衬底具有相同晶格排列的单晶材料,
外延层可以是同质外延层(Si/Si),也可以是异质外延层(SiGe/Si 或SiC/Si等);同样实现外延生长也有很多方法,包括分子束外延(MBE),超高真空化学气相沉积(UHV/CVD),常压及减压外延(ATM &RP Epi)等等。本文仅介绍广泛应用于半导体集成电路生产中衬底为硅材料的硅(Si)和锗硅(SiGe)外延工艺。根据生长方法可以将外延工艺分为两大类(表1):全外延(Blanket Epi)和选择性外延(Selective Epi, 简称SEG)。工艺气体中常用三种含硅气体源:硅烷(SiH4),二氯硅烷(SiH2Cl2, 简称DCS) 和三氯硅烷(SiHCl3, 简称TCS);某些特殊外延工艺中还要用到含Ge和C的气体锗烷(GeH4)和甲基硅烷(SiH3CH3);选择性外延工艺中还需要用到刻蚀性气体氯化氢(HCl),反应中的载气一般选用氢气(H2)。
外延选择性的实现一般通过调节外延沉积和原位(in-situ)刻蚀的相对速率大小来实现,所用气体一般为含氯(Cl)的硅源气体DCS,利用反应中Cl原子在硅表面的吸附小于氧化物或者氮化物来实现外延生长的选择性;由于SiH4不含Cl原子而且活化能低,一般仅应用于低温全外延工艺;而另外一种常用硅源TCS蒸气压低,在常温下呈液态,需要通过H2鼓泡来导入反应腔,但价格相对便宜,常利用其快速的生长率(可达到5 um/min)来生长比较厚的硅外延层,这在硅外延片生产中得到了广泛的应用。IV族元素中Ge的晶格常数(5.646A与Si的晶格常数(5.431A差别最小,这使得SiGe与Si工艺易集成。在单晶Si中引入Ge形成的SiGe单晶层可以降低带隙宽度,增大晶体管的特征截止频率fT(cut-off frequency),这使得它在无线及光通信高频器件方面应用十分广泛;另外在先进的CMOS集成电路工艺中还会利用Ge跟Si的晶格常数失配(4%)引入的晶格应力来提高电子或者空穴的迁移率(mobility),从而增大器件的工作饱和电流以及响应速度,这正成为各国半导体集成电路工艺研究中的热点。由于本征硅的导电性能很差,其电阻率一般在200ohm-cm以上,通常在外延生长的同时还需要掺入杂质气体(dopant)来满足一定的器件电学性能。杂质气体可以分为N型和P型两类:常用N型杂质气体包括磷烷(PH3)和砷烷(AsH3),而P型则主要是硼烷(B2H6)。硅及锗硅外延工艺在现代集成电路制造中应用十分广泛,概括起来主要包括:1.硅衬底外延:
硅片制造中为了提高硅片的品质通常在硅片上外延一层纯净度更高的本征硅;或者在高搀杂硅衬底上生长外延层以防止器件的闩锁(latch up)效应。2.异质结双极晶体管(Hetero-junction Bipolar Transistor,简称HBT)基区(base)异质结SiGe外延(图1):其原理是在基区掺入Ge组分,通过减小能带宽度,从而使基区少子从发射区到基区跨越的势垒高度降低,从而提高发射效率γ, 因而,很大程度上提高了电流放大系数β。在满足一定的放大系数的前提下,基区可以重掺杂,并且可以做得较薄,这样就减少了载流子的基区渡越时间,从而提高器件的截止频率fT (Cut-Off Frequency),这正是异质结在超高速,超高频器件中的优势所在。
3.CMOS源(source)漏(drain)区选择性Si/SiGe外延:进入90nm工艺时代后,随着集成电路器件尺寸的大幅度减小,源漏极的结深越来越浅,需要采用选择性外延技术 (SEG)以增厚源漏极(elevated source/drain)来作为后续硅化(silicide)反应的牺牲层(sacrificial layer) (图2),从而降低串联电阻,有报道称这项技术导致了饱和电流(Idsat)有15%的增加。
而对于正在研发中的65/45nm技术工艺,有人采用对PMOS源漏极刻蚀后外延SiGe层来引入对沟道的压应力(compressive stress) (图3),以提高空穴(hole)的迁移率(mobility),据报道称实现了饱和电流(Idsat)35%的增加。
应变硅(strain silicon)外延:在松弛(relaxed)的SiGe层上面外延一层单晶Si,由于Si跟SiGe晶格常数失配而导致Si单晶层受到下面SiGe层的拉伸应力(tensile stress)而使得电子的迁移率(mobility)得到提升(图4),这就使得NMOS在保持器件尺寸不变的情况下饱和电流(Idsat)得到增大,而Idsat的增大意味着器件响应速度的提高,这项技术正成为各国研究热点。一般而言,一项完整的外延工艺包括3个环节:首先,根据需要实现的工艺结果对硅片进行预处理,包括去除表面的自然氧化层及硅片表面的杂质,对于重搀杂衬底硅片则必须考虑是否需要背封(backseal)以减少后续外延生长过程中的自搀杂。然后在外延工艺过程中需要对程式进行优化,如今先进的外延设备一般为单片反应腔,能在100秒之内将硅片加热到1100℃以上,利用先进的温度探测装置能将工艺温度偏差控制在2度以内,反应气体则可通过质量流量计(MFC)来使得流量得到精准控制。在进行外延沉积之前一般都需要H2烘烤(bake)这一步,其目的在于原位(in-situ)去除硅片表面的自然氧化层和其他杂质,为后续的外延沉积准备出洁净的硅表面状态。 最后在外延工艺完成以后需要对性能指标进行评估,简单的性能指标包括外延层厚度和电特性参数, 片内厚度及电特性均匀度(uniformity),片与片间的重复性(repeatability),杂质颗粒(particle)数目以及污染(contamination);在工业生产中经常要求片内膜厚及电性的均匀度<1.5%(1σ),对硅片厂家来说经常还要考查外延层的扩展电阻率曲线(SRP)以确定是否有污染存在及污染物杂质的量。特别地,对于SiGe工艺我们经常还需要测量Ge的含量及其深度分布,对于有搀杂的工艺我们还需要知道搀杂原子的含量及深度分布。另外晶格缺陷(defect)也是我们必须考虑的问题,一般而言,常常出现的有四种缺陷,包括薄雾(haze),滑移线(slip line), 堆跺层错(stacking fault) 和穿刺(spike),这些缺陷的存在对器件性能有很大影响,可以导致器件漏电流增大甚至器件完全失效而成为致命缺陷(killer effect)。一般来讲消除这些缺陷的办法是检查反应腔体漏率是否足够低(<1mTorr/min),片内工艺温度分布是否均匀,承载硅片的基座或准备的硅片表面是否洁净、平坦等。经过外延层性能指标检测以后我们还需要对外延工艺进一步优化,以满足特定器件的工艺要求。硅衬底外延:硅片制造中为了提高硅片的品质通常在硅片上外延一层纯净度更高的本征硅;或者在高搀杂硅衬底上生长外延层以防止器件的闩锁(latch up)效应。.太阳能级硅的纯度更高
多晶硅的生产工艺:从西门子法到改良西门子法
从西门子法到改良西门子法的演进是一个从开环到闭环的过程。
1955年,德国西门子开发出以氢气(H2)还原高纯度三氯氢硅(SiHCl3),在加热到1100℃左右的硅芯(也称“硅棒”)上沉积多晶硅的生产工艺;1957年,这种多晶硅生产工艺开始应用于工业化生产,被外界称为“西门子法”。
由于西门子法生产多晶硅存在转化率低,副产品排放污染严重(例如四氯化硅SiCl4)的主要问题,升级版的改良西门子法被有针对性地推出。改良西门子法即在西门子法的基础上增加了尾气回收和四氯化硅氢化工艺,实现了生产过程的闭路循环,既可以避免剧毒副产品直接排放污染环境,又实现了原料的循环利用、**降低了生产成本(针对单次转化率低)。因此,改良西门子法又被称为“闭环西门子法”。
改良西门子法一直是多晶硅生产最主要的工艺方法,目前全世界有超过85%的多晶硅是采用改良西门子法生产的。过去很长一段时间改良西门子法主要用来生产半导体行业电子级多晶硅(纯度在99.9999999%~99.999999999%,即9N~11N的多晶硅);光伏市场兴起之后,太阳能级多晶硅(对纯度的要求低于电子级)的产量迅速上升并**超过了电子级多晶硅,改良西门法也成为太阳能级多晶硅最主要的生产方法。
2.改良西门子法生产多晶硅的工艺流程
(改良西门子法工艺流程示意图)
改良西门子法是一种化学方法,首先利用冶金硅(纯度要求在99.5%以上)与氯化氢(HCl)合成产生便于提纯的三氯氢硅气体(SiHCl3,下文简称TCS),然后将TCS精馏提纯,最后通过还原反应和化学气相沉积(CVD)将高纯度的TCS转化为高纯度的多晶硅。
在TCS还原为多晶硅的过程中,会有大量的剧毒副产品四氯化硅(SiCl4,下文简称STC)生成。改良西门子法通过尾气回收系统将还原反应的尾气回收、分离后,把回收的STC送到氢化反应环节将其转化为TCS,并与尾气中分离出来的TCS一起送入精馏提纯系统循环利用,尾气中分离出来的氢气被送回还原炉,氯化氢被送回TCS合成装置,均实现了闭路循环利用。这是改良西门子法和传统西门子法最大的区别。
CVD还原反应(将高纯度TCS还原为高纯度多晶硅)是改良西门子法多晶硅生产工艺中能耗最高和最关键的一个环节,CVD工艺的改良是多晶硅生产成本下降的一项重要驱动力。
3.与主要生产工艺的比较
改良西门子法在多晶硅生产领域已经应用了几十年,至今它的主导地位仍然牢不可破。通过CVD技术的改良、中间气体生产技术的进步和规模化效益的凸显,
TC是Thermocouple的缩写,是你在测温板上的测试位置,最高上升斜率就是从炉子入口到最高温度的最大的上升斜率(每秒上升的温度),最高下降斜率是从最高温度到停止温度的最大下降斜率,PWI是Process Window Index缩写,工艺窗口指数,是KIC的专利,PWI能够快速显示测试曲线的合格性,就连小学生也可快速判断曲线是否合格。这些统计数据其实就是从进入炉子内部到出口的整个焊接工艺过程,所以当我们在测试过程中就能够获得这组数据并进行工艺分析是否能够满足当前产品的工艺窗口要求。KIC测温仪能够告知用户如何测试一个合格的曲线,并告诉用户如何设定和优化温度参数,且能够快速告诉曲线的合格性。
随着工业4.0的发展,很多公司都已经在上MES系统了,在印刷机,贴片机,AOI都已经实现了自动化,唯独回流焊还是每天人工测试曲线,而且很多人都只是关注贴片机,印刷机等产生的不良品,疏而不知回流焊也是一个重大品质隐患的重要工序,印刷机有SPI,贴片机有AOI监控,而回流焊呢?BGA内部呢?
为了解决这一个难题,建议使用UPVIEW自动测温曲线系统,这是一款用于SMT,半导体等领域的自动测温曲线系统,由传统每天人工测试变为自动测试曲线,并实现一片板测试一个曲线152,使所有产品工艺的一致性和品质管控2019,以及降低人工和生产成本3608。为回流焊实现自动化测试和智能工厂及MES起到重要作用。如果需要更多技术资料获取请直接+前面的数字。
UPVIEW自动测温曲线系统
主要功能:
1. 自动测试每一片板温度曲线:确保所有产品工艺品质和一致性。
2. 实时SPC图表统计和CPK计算:实时监测整个工艺的趋势,一旦发生异常变化自动报警。
3. 条码绑定曲线可追溯性:自动将条码绑定每个产品曲线以便后续进行追溯。
4. 实时工艺曲线数据输出连接MES:实时输出数据给MES进行大数据收集和分析
5. 实时监测炉内温度和速度变化量:直观显示每片产品在经过炉内各温区温度和速度变化
6. 工艺异常自动警报:出现工艺异常时,系统自动报警并自动断开PCB进入炉内起到品质管控作用。
7. 所有炉子远程集中管理:实时远程监控所有炉子生产状态一目了然,减少人员配置和异常及时处理
8. 实时O2氧含量记录追踪:实时O2氧含量绑定工艺曲线便于后续追踪。
主要改善:
降低人工测试工时成本
降低制作测温板成本和辅料成本
降低人为误 *** 作风险
消除设备停线时间
消除人工测试的局限性
提高生产效率 和产品品质
智能自动化测试曲线(1片板1曲线)
产品可追溯性
评论列表(0条)