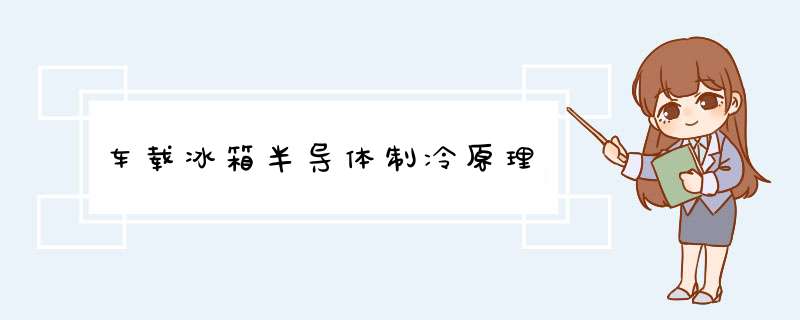
车载小冰箱的
半导体制冷原理 半导体制冷技术 材料是当今世界的三大支柱产业之一,材料是人类赖以生存和发展的物质基础,尤其是近几十年来随着人类科学技术的进步,材料的发展更是日新月异,新材料层出不穷,其中半导体制冷材料就是其中的一个新兴的热门材料,其实半导体制冷技术早在十九世纪三十年代就已经出现了,但其性能一直不尽如人意,一直到了二十世纪五十年代随着半导体材料的迅猛发展,热点制冷器才逐渐从实验室走向工程实践,在国防、工业、农业、医疗和日常生活等领域获得应用,大到可以做核潜艇的空调,小到可以用来冷却红外线探测器的探头,因此通常又把热电制冷器称为半导体制冷器。 半导体制冷器件大致可以分为四类: (1)用于冷却某一对象或者对某个特定对象进行散热,这种情况大量出现在电子工业领域中; (2)用于恒温,小到对个别电子器件维持恒温 ,大到如制造恒温槽,空调器等(3)制造成套仪器设备,如环境实验箱,小型冰箱,各种热物性测试仪器等(4)民用产品,冷藏烘烤两用箱,冷暖风机等。 半导体制冷的应用: (1)在高技术领域和军事领域 对红外探测器,激光器和光电倍增管等光电器件的制冷。比如,德国Micropelt公司的半导体制冷器体积非常小,只有1个平方毫米,可以和激光器一起使用TO封装。 (2)在农业领域的应用 温室里面过高或过低的温度,都将导致秧苗坏死,尤其部分名贵植物对环境更加敏感,迫切需要将适宜的温度检测及控制系统应用于现代农业。 (3)在医疗领域中的应用 半导体温控系统在医学上的应用更为广泛。如:用于蛋白质功能研究、基因扩增的高档PCR仪、电泳仪及一些智能精确温控的恒温仪培养箱等;用于开发具有特殊温度平台的扫描探针显微镜等。 半导体制冷的优点 半导体制冷器的尺寸小,可以制成体积不到1cm小的制冷器;重量轻,微型制冷器往往能够小到只有几克或几十克。无机械传动部分,工作中无噪音,无液、气工作介质,因而不污染环境,制冷参数不受空间方向以及重力影响,在大的机械过载条件下,能够正常地工作通过调节工作电流的大小,可方便调节制冷速率;通过切换电流方向,可是制冷器从制冷状态转变为制热工作状态;作用速度快,使用寿命长,且易于控制。 半导体制冷器件的工作原理 半导体制冷器件的工作原理是基于帕尔帖原理,该效应是在1834年由J.A.C帕尔帖首先发现的,即利用当两种不同的导体A和B组成的电路且通有直流电时,在接头处除焦耳热以外还会释放出某种其它的热量,而另一个接头处则吸收热量,且帕尔帖效应所引起的这种现象是可逆的,改变电流方向时,放热和吸热的接头也随之改变,吸收和放出的热量与电流强度I[A]成正比,且与两种导体的性质及热端的温度有关,即: Qab=Iπab πab称做导体A和B之间的相对帕尔帖系数 ,单位为[V], πab为正值时,表示吸热,反之为放热,由于吸放热是可逆的,所以πab=-πab 帕尔帖系数的大小取决于构成闭合回路的材料的性质和接点温度,其数值可以由赛贝克系数αab[V.K-1]和接头处的绝对温度T[K]得出πab=αabT与塞贝克效应相,帕尔帖系也具有加和性,即: Qac=Qab+Qbc=(πab+πbc)I 因此绝对帕尔帖系数有πab=πa- πb 金属材料的帕尔帖效应比较微弱,而半导体材料则要强得多,因而得到实际应用的温差电制冷器件都是由半导体材料制成的。 半导体制冷材料的发展 AVIoffe和AFIoffe指出,在同族元素或同种类型的化合物质间,晶格热导率Kp随着平均原子量A的增长呈下降趋势。RWKeyes通过实验推断出,KpT近似于Tm3/2ρ2/3A-7/6成比例,即近似与原子量A成正比,因此通常应选取由重元素组成的化合物作为半导体制冷材料。 半导体制冷材料的另一个巨大发展是1956年由AFIoffe等提出的固溶体理论,即利用同晶化合物形成类质同晶的固溶体。固溶体中掺入同晶化合物引入的等价置换原子产生的短程畸变,使得声子散射增加,从而降低了晶格导热率,而对载流子迁移率的影响却很小,因此使得优值系数增大。例如50%Bi2Te3-50%Bi2Se3固溶体与Bi2Te3相比较,其热导率降低33%,而迁移率仅稍有增加,因而优值系数将提高50%到一倍。 Ag(1-x)Cu(x)Ti Te、Bi-Sb合金和YBaCuO超导材料等曾经成为半导体制冷学者的研究对象,并通过实验证明可以成为较好的低温制冷材料。下面将分别减少这几种热电性能较好的半导体制冷材料。 二元Bi2Te3-Sb2Te3和Bi2Te3-Bi2Se3固溶体 二元固溶体,无论是P型还是N型,晶格热导率均比Bi2Te3有较大降低,但N型材料的优值系数却提高很小,这可能是因为在Bi2Te3中引入Bi2Se3时,随着Bi2Se3摩尔含量的不同呈现出两种不同的导电特性,势必会使两种特性都不会很强,通过合适的掺杂虽可以增强材料的导电特性,提高材料的优值系数,但归根结底还是应该在本题物质上有所突破。 三元Bi2Te3-Sb2Te3-Sb2Se3固溶体 Bi2Te3 和Sb2Te3是菱形晶体结构,Sb2Se3是斜方晶体结构,在除去大Sb2Se3浓度外的较宽组份范围内,他们可以形成三元固溶体。无掺杂时,此固溶体呈现P型导电特性,通过合适的掺杂,也可以转变为N型导电特性。在二元固溶体上添加Sb2Se3有两个优点:首先是提高了固溶体材料的禁带宽度。其次是可以进一步降低晶格热导率,因此Sb2Se3不论是晶体结构还是还是平均原子量,都与Bi2Te3 和Sb2Te3相差很大。当三元固溶体中Sb2Te3+5% Sb2Se3的总摩尔含量在55%~75%范围时,晶格热导率最低,约为0.8×10-2W/cm K,这个值要略低于二元时的最低值0.9×10-2W/cm K。 但是,添加Sb2Se3也会降低载流子的迁移率,将会降低优值系数,因此必须控制Sb2Se3的含量。 P型Ag(1-x)Cu(x)Ti Te材料 AgTi Te材料由于具有很低的热导率(k=0.3 W/cm K),因此如能通过合适的掺杂提高其载流子迁移率μ和电导率σ,将有可能得到较高的优值系数Z。RMAyral-Marin等人通过实验研究,发现将AgTi Te和CuTi Te通过理想的配比形成固溶体,利用Cu原子替换掉部分Ag原子后,可以得到一种性能较好的P型半导体制冷材料Ag(1-x)Cu(x)Ti Te,其中x在0.3左右时,材料的热电性能最好。由此可见Ag(1-x)Cu(x)Ti Te的确是一种较好的P型半导体制冷材料。 N型Bi-Sb合金材料 无掺杂的Bi-Sb合金是目前20K到220K温度凡内优值系数最高的半导体制冷材料,其在富Bi区域内为N型,而当Sb含量超过75%时将转变为P型。在Bi的单晶体中引入Sb,没有改变晶体结构,也没有改变载流子(包括电子和空穴)浓度,但是拉大了导带和禁带之间的宽度。Sb的含量为0~5%时禁带宽度约为0eV,即导带和禁带相连,属于半金属;Sb含量在5%~40%时,禁带宽度值基本是在0.005eV左右,当Sb的含量在12%~15%时,达到最大,约为0.014eV,属于窄带本征半导体。由上文所述,禁带宽度的增加必将提高材料的温差电动势。80K到110K温度范围内,是Bi85Sb15的优值系数最高,高温时则是Bi92Te8最高。 YBaCuO超导材料 根据上面的介绍可知,在50K到200K的温度范围内,性能最好的半导体制坑材料是n型Bi(100-x)Sbx合金,其中Sb的含量在8%~15%。在100K零磁场的情况下,Bi-Sb合金的最高优值系数可达到6.0×10-3K-1,而基于Bi、Te的p型固溶体材料在100K时的优值系数却低于2.0×10-3K-1并且随着温度的下降迅速减小。因此,必须寻找一种新的p型低温热电材料,以和n型Bi-Sb合金组成半导体制冷电对。利用高Tc氧化物超导体代替p型材料,作为被动式p型电臂(称为HTSC臂,即High Tc Supercon-ducting Legs),理论上可以提高电队的优值系数,经过实验证明也确实可行。半导体制冷电对在器件两臂满足最佳截面比时的最佳优值系数为: zmax= (1)式中的下标p和n分别对应p型材料和n型材料。由于HTSC超导材料的温差电动势率α几乎为零,但其电导率无限大,因此热导率κ和电导率δ的比值κ/δ却是无限小的,这样式(1)可以简化为: zmax(HTSC)=即由n型热电材料和HTSC臂所组成的制冷电对的优值系数,将等于n型材料的优值系数。 Mosolov A B等人分别利用以SrTiO3座基地的YBaCuO超导薄膜和复合YBaCuO-Ag超导陶瓷片作为被动式HTSC臂材料,用Bi91Sb9合金作为n型材料,制成单级半导体制冷器。实验结果表明:利用YBaCuO超导薄膜制成的制冷器,热端温度维持在85K,零磁场时可达到9.5K的最大制冷温差,加上0.07T横向磁场时能达到14.4K利用YBaCuO-Ag超导陶瓷片制成的单击制冷器,热端温度维持在77K时,相应的最大制冷温差分别是11.4K和15.7K。从半导体制冷器最大制冷温差计算公式,可以反算出80Kzuoyou这种制冷电对的优值系数约为6.0×10-3K-1,可见这种电对组合是有着很好的应用潜力的。随着高Tc超导体材料的发展,这种制冷点队的热端温度将会逐渐提高,优值系数也将逐渐增大,比将获得跟广泛的应用。半导体制冷效率的大小取决于热电堆冷热端的温差,而强化热端的散热与强化冷端的冷量散发有利于降低热电堆冷热端的温差,从而提高半导体的制冷效率.本文探讨了由半导体冷端提供冷量进行制冷的空间温度在自然对流和强制对流状态下随时间变化的规律.结果表明强制对流有助于冷量的传递和制冷效率的提高.
http://www.hahan.org/papers/chemistry/123412.html
http://auto.search.msn.com/response.asp?MT=%E5%A6%82%E4%BD%95%E5%A2%9E%E5%BC%BA%E5%8D%8A%E5%AF%BC%E4%BD%93%E5%86%B0%E7%AE%B1%E7%9A%84%E5%88%B6%E5%86%B7&srch=3&prov=&utf8
我们在 ExtremeTech 上讨论了很多半导体工艺节点,但是从技术上讲,我们并不经常提及什么是半导体工艺节点 。 随着 Intel 的 10nm 节点进入生产阶段,对于半导体工艺节点的困惑越来越多了,而且对于台积电和
三星的技术是不是优于英特尔(以及如果拥有的优势,他们拥有多少优势),也打上了问号。
半导体工艺节点通常以数字命名,后跟纳米的缩写:32nm,22nm,14nm等。CPU 的任何功能与节点名称之间没有固定的客观联系。半导体工艺节点的命名方式也并非总是如此,在大约 1960s-1990s ,节点是根据门的长度来命名的。IEEE 的这张图显示了这种关系:
长期以来,栅极长度(晶体管栅极的长度)和半间距(芯片上两个相同特征,如栅级,之间的距离的一半)与过程节点名称相匹配,但最后一次是 1997年 。半间距又连续几代与节点名匹配,但在实际意义上两者并没有什么关系。实际上,特征尺寸和芯片实际上的样子匹配,已经是很长很长时间之前的事情了。
如果我们达到几何比例缩放要求以使节点名称和实际特征尺寸保持同步,那么六年前我们就该将生产线降至 1nm 以下(这怎么可能嘛)。我们用来表示每个新节点的数字只是代工厂为了宣传选取的数字。早在2010年,ITRS(国际半导体技术发展蓝图,稍后对此组织进行详细介绍)把在每个节点上应用的技术集称为“等效扩展”(而不是几何扩展)。当我们接近纳米级的极限时,宣传可能会开始使用埃而不是纳米,或者可能会使用小数点。当我开始在这个行业工作时,通常会看到记者提到微米而不是纳米的工艺节点,例如 0.18微米或 0.13微米,而不是 180nm 或 130nm。
半导体制造涉及大量的资本支出和大量的长期研究。从论文采用新技术到大规模商业化生产之间的平均时间间隔为10到15年。几十年前,半导体行业认识到,如果存在针对节点引入的通用路线图以及这些节点所针对的特征尺寸,这对每个电子工业的参与方都是有利的。这将允许生产线上的不同位置的厂商同时克服将新节点推向市场遇到的难题。多年来,ITRS(国际半导体技术路线图)一直在发布该行业的总体路线图。这些路线图长达15年之久,为半导体市场设定了总体目标。
ITRS于1998-2015年发布。从2013年至2014年,ITRS重组为ITRS 2.0,他们很快意识到传统的推进方法遇到了理论创新的瓶颈,新组织的任务目标是为大学、财团和行业研究人员提供“未来的主要参考方向,以激发技术各个领域的创新”,这个目标也要求新组织大幅扩展其覆盖范围和覆盖范围。ITRS就此宣布退休了,成立了一个新的组织,称为IRDS(国际设备和系统路线图),其研究的范围大得多,涉及更广泛的技术。
范围和重点的转移反映了整个代工行业正在发生的事情。我们停止将栅极长度或半间距与节点大小绑定的原因是,它们要么停止缩小,要么缩小的速率减慢。作为替代方案,公司已经集成了各种新技术和制造方法,从而继续进行节点缩放。在40 / 45nm,GF和TSMC等公司推出了浸没式光刻技术。在32nm处引入了双图案。后栅极制造是28nm的功能。FinFET是由Intel在22nm处引入的,而其他公司则是在14 / 16nm节点处引入的。
公司有时会在不同的时间推出功能。AMD和台积电推出了40 / 45nm浸没式光刻技术,但英特尔等到32nm才使用该技术,并选择首先推出双图案。GlobalFoundries和台积电开始在32 / 28nm使用更多的双图案。台积电在28nm处使用后栅极构造,而三星和GF使用先栅极技术。但是,随着进展变得越来越慢,我们已经看到公司更加依赖于营销,拥有更多定义的“节点”。像三星这样的公司,没有像以前一样瀑布式下降节点名字(90、65、45),而是给不同的工艺节点起了数字部分相同的名字:
我认为您可以吐槽该产品名称不明不白,因为除非您有清晰的图表,否则很难分辨哪些流程节点是早期节点的演变变体。
尽管节点名称不 依赖 于任何特征尺寸,并且某些特征尺寸已停止缩小,但半导体制造商仍在寻找改善关键指标的方法。这是真正的技术进步。但是,由于现在很难获得性能上的优势,并且更小的节点需要更长的开发时间,因此公司正在尝试更多所谓的改进实验。例如,三星正在准备比以前更多的节点名称。那是某种营销策略,而不是他们真的能做出来多么超前的改进。
因为英特尔10纳米制程的制造参数非常接近台积电和三星用于7纳米制程的值。下面的图表来自WikiChip,但它结合了英特尔10nm节点的已知功能尺寸和台积电和三星7nm节点的已知功能尺寸。如您所见,它们非常相似:
delta 14nm / delta 10nm列显示了每个公司从其上一个节点开始将特定功能缩小的程度。英特尔和三星的最小金属间距比台积电更严格,但是台积电的高密度SRAM单元比英特尔小,这可能反映了台湾代工厂的不同客户的需求。同时,三星的单元甚至比台积电的单元还要小。总体而言,英特尔的10nm工艺达到了许多关键指标,台积电和三星都将其称为7nm。
由于特定的设计目标,单个芯片可能仍具有偏离这些尺寸的功能。制造商提供的这些数字是给定节点上的典型预期实现方式,不一定与任何特定芯片完全匹配。
有人质疑英特尔的10nm +工艺(用于Ice Lake)在多大程度上达到了这些宣传的指标(我相信这些数字是针对Cannon Lake发布的)。的确,英特尔10纳米节点的预期规格可能会略有变化,但14纳米+也是14纳米的调整,10nm+肯定比14nm工艺有非常大的改进。英特尔已经表示,一定会把10nm工艺节点的晶体管密度相对14nm增加2.7倍作为目标,因此我们将推迟任何有关10nm +可能略有不同的猜测。
理解新流程节点的含义的最佳方法是将其视为总括性术语。当一家代工厂商谈论推出一个新的流程节点时,他们所说的其实是:
“我们创建了具有更小特征和更严格公差的新制造工艺。为了实现这一目标,我们集成了新的制造技术。我们将这组新的制造技术称为流程节点,因为我们想要一个总括的术语,向大众传递我们改进了某些具体的工艺参数。”
关于该主题还有其他问题吗?将它们放到下面,我会回答他们。
评论列表(0条)