本应用笔记给出了一个简单的外部电路,它能将初始电流尖峰降至最小并在200至500ns内隔离短路故障。
典型热插拔电路 我们来考察采用MAX4272构建的+12V、6A典型热插拔控制电路(图1)。根据MAX4272的规格指标,可知其包含触发门限分别为50mV和200mV的低速和快速比较器(整个温度范围内,容限分别为43.5mV至56mV和180mV至220mV)。触发电流大小通常为工作电流的1.5至2.0倍,选择RSENSE = 5mΩ。RSENSE允许有5%的容限,过载条件下低速比较器的触发电流范围是8.28至11.76A;发生短路时,快速比较器的触发电流范围是34A至46.2A。
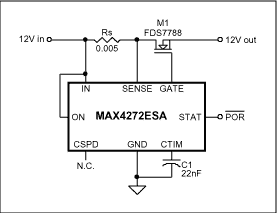
图1. 典型的热插拔控制电路
低速比较器的最低触发门限比正常工作电流高38%,快速比较器的短路触发门限是工作电流的6至8倍。
快速比较器的延迟时间为350ns,这一时段的短路电流尖峰仅受限于电路阻抗。此后电流缓慢下降,直至完全隔离短路故障,3mA栅极下拉电流限制了MOSFET M1栅极电容(3nF至4nF)的放电速率。短路电流在15µs至40µs内缓慢减小,与此同时,栅极电压从19V被拉到接近地电位。 峰值短路电流 最初350ns内的峰值电流由以下因素决定:
(a) 电源ESR,(b) 短路状态,(c) RSENSE阻值,(d) M1的RDS(ON),(e) M1的ID(ON)。
以上参数均采用最接近实际情况的取值,可以计算出短路时电路的总阻抗:
(电源ESR ≈ 4mΩ) + (短路环节 ≈ 3mΩ) + (RSENSE = 5mΩ) + (RD(ON) ≈ 4mΩ) ≈ 16mΩ。
这时,短暂的峰值电流为:ISC ≈ 750A,并取决于电源的储能电容(带2200µF电容的低ESR背板以750A电流放电时,1µs内电压仅降低340mV)。这种情况下,实际的峰值ISC会由M1的ID(ON)限制到400A左右。
ID(ON)取决于VGS,因此有必要检查电路,以确定这一时段的栅-源电压。MAX4272包含一个内部电荷泵,可使正常工作时的栅极电压高出VIN约7V。因而MOS管导通时VGS = 7V。
短路的第二个影响是它实际上增加了VGS。短路在M1的漏-源之间引入了一个电压阶跃 -等于总输入电压的一部分。由于M1的RD(ON)约为预估的短路总阻抗的1/3,此时施加的VDS约为12V阶跃电压的1/3。由漏-栅电容cdg和栅-源电容cgs组成的分压器会将该阶跃电压的一部分转移到栅极。经过适当计算,可知引入的额外ΔVGS为300mV至500mV,但短路期间进行的测试表明该值可高达ΔVGS = +3V。
至此可以清楚地看出,牢固可靠的短路会在几微秒至几十微秒内产生数百安培的电流。
设计者可能希望将ISC峰值限制在50A,持续时间小于1µs,但如果不增加更快速的比较器和栅极下拉电路的话,这一要求是不切实际的。然而,可以考虑对电路做一些简单的修改。
- 在内部快速比较器最初的350ns响应时间内,电流会由ID(ON)限制在几百安以内,此时可以通过增加一个简单的外部电路来加快栅极放电,从而将短路持续时间限制≤ ½µs。
- 或者用一个稍复杂的外部电路将Isc峰值限制在100A范围内,并且持续时间≤ 200ns。
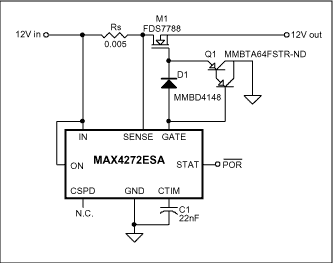
图2. 具有快速栅极下拉的热插拔控制器 快速限流电路 借助图3所示的电路,可以将短路电流限制在约100A以下,持续时间小于200ns。当RSENSE两端的电压差达到约600mV时,PNP型晶体管Q1a将触发并驱动NPN型晶体管Q1b,从而使M1的栅极电容快速放电。
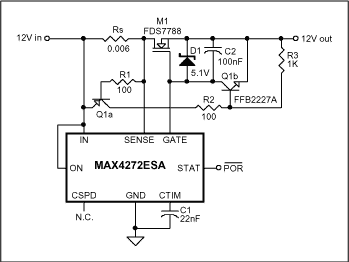
图3. 具有快速短路峰值电流限制功能的热插拔控制器
M1栅极和源极之间的C2可进一步减小发生短路时作用在栅极上的正向瞬态阶跃电压,该电容的取值范围为10nF至100nF。
齐纳二极管D1用来将VGS限制到7V (MAX4272提供该电压)以下的某个值。
虽然齐纳二极管D1在偏置电流为5mA时的额定值为5.1V,但在本电路中,MAX4272仅能输出100µA的栅极充电电流(齐纳二极管偏置电流),因此D1会将VGS限制在3.4V左右。受到限制的VGS可降低ID(ON),当然RD(ON)会增大一些。根据MOS管的数据资料可知:VGS为3.4V时RD(ON)为5mΩ,VGS为7V时RD(ON)为3mΩ。这样可以更快地关断M1。
D1和C2也可以用在图1和图2的电路中,以降低短路时的ID(ON)。 测试方法-造成短路 没有什么比制造短路更简单了。
但要产生牢固可靠并且重复性较好的短路情况非常富有挑战性。本测试对以下几种制造短路的方法进行了评估。
- 机械开关闭合时总会出现几毫秒的触点抖动过程。旋转式多触点开关似乎可以避免类似情况发生,但由于多次大电流闭合所形成的电火花会腐蚀触点,因此开关的重复性令人怀疑。
- 大电流继电器触点闭合时也会产生抖动,并且会表现出不同的闭合电阻。
- 实验证明,可控硅整流器的电流上升速率不尽人意。
- 大电流汞位移继电器是人们寄予厚望的最佳方法,但结果并不令人满意。一个标称阻抗4mΩ的60A、600V汞继电器在刚开始接触时阻抗为40mΩ,随着电流脉冲流过15µs后会轻松降至4mΩ。
- 手工短路 *** 作可提供一种随意的、断续并且非重复性的短接方式,具有较强的随机性!可以获得非常陡的电流波前沿。综上所述,尽管触点腐蚀对每次闭合的重复性有影响,但这种方法仍是最有效(和最经济)的。
如果在实验室里通过机械手段,来始终如一地产生带陡峭电流波前的真正低阻短路故障极为困难。电路工作时几乎肯定会经历这种意外短路故障。
通常人为制造短路将产生如图4所示的电容放电电流和电压波形。上方曲线是选择5V/div档位时记录的短路输出电压, 可以看出大部分时间(25µs/div)内电容放电不足一半。下方曲线是选择25A/div档位时记录的短路电流,可清楚地显示出接触是断断续续的。
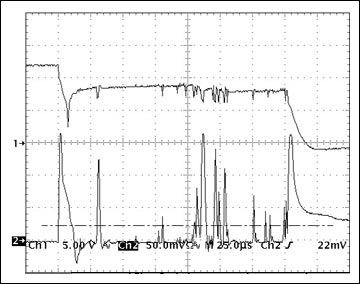
图4. 不规则的机械短路信号波形
构建ESR低于5mΩ的电源也不容易。尽管如此,仍竭尽全力构建了一个低ESR (4–5mΩ)的电压源,经细心测量,可知在100A短路情况下电压下降440mV。该电压源的输入端直接并联了1个5500µF的计算机等级电解电容、1个3.3µF多层陶瓷电容以及6个100µF专业聚合物铝电解电容,并由1个10A电源驱动。 短路电流波形 图1所示电路(未作改进)的短路电流波形如图5所示。由于测量的是电流检测电阻RS两端的电压,并且示波器地与测试电路的+12V输入端相连,因此信号波形看上去是反相的。RS为6mΩ,电压档位选择1V/div,峰值电压为2400mV或400A。电流波前并不像接触良好时一样陡峭。
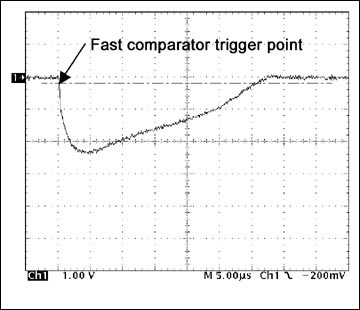
图5. 电路未作改动时具有400A峰值短路电流
观察图6所示的电压信号波形有助于加深理解,图中给出了短路时的输出电压、M1栅极电压波形以及RS两端的电压。所有电压均以+12V输入为参考。
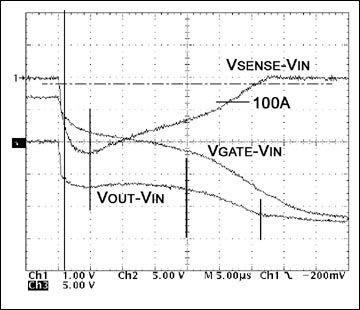
图6. 电路未作改动时的短路电压和电流波形
VOUT - VIN信号波形显示,短路期间VOUT下降了7V,这表明短路阻抗只略低于总电路阻抗的½。更低阻抗的短路故障会产生高于400A的峰值电流。信号波形还表明在开始的300ns内短路不是完全牢固可靠;这导致了VSENSE信号波形缓慢下落。
由VGATE波形可以看出,最初VGS = 7V,由于VOUT下降,1µs后增至10V左右。5µs后VGS仅降至9V,20µs时降至6V,33µs时降至4V。由于放电电流仅为3mA,因此栅极放电缓慢。这样一来,发生短路故障后27µs内短路电流仍为100A。
图2的快速栅极下拉电路不大会降低最初的短路电流,但PNP型达林顿管下拉会迅速终止电流信号波形。这种配置下的短路电流信号波形如图7所示,峰值电流仍为2400mV或400A,但快速比较器在370ns触发后,电流可在50ns内阻断。还应注意,短路电流信号波形是非常陡峭的,表明机械短路非常可靠。
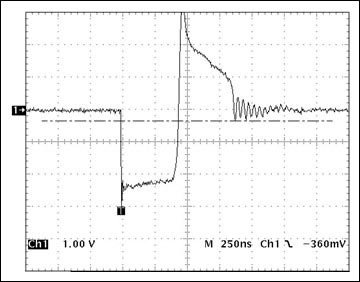
图7. 快速下拉电路的短路电流波形
当电路电容给输入电容充电时电源电流发生反向,并导致+12V输入端出现一个小幅正向过冲。
图3的快速短路峰值电流限制电路在限制峰值电流以及短路电流持续时间方面均有效。如图8所示,RS (6mΩ)两端的电压峰值为600mV,对应100A峰值电流。短路电流阻断极其迅速,电流脉冲在200ns内完全终止。
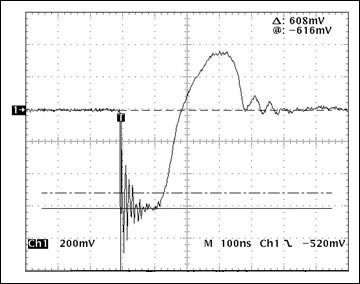
图8. 改进后热插拔控制器电路的短路电流脉冲
利用该技术可将背板电源干扰降至最低,如图9所示,会在测试方法一节中提到的+12V电源上产生小于±500mV的峰值电压干扰。
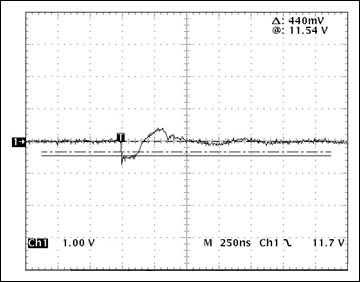
图9. 图3电路发生短路时引起的背板干扰
再次看到陡峭的电流波前,表明这是一个质量非常高的短路状态。遗憾的是,很难复现这样的陡峭电流波形。 那么发生了什么? PNP-NPN检测/下拉电路终止短路电流(然后解除控制)如此迅速,以至于MAX4272快速比较器没有足够的时间触发(响应时间 = 350ns)。图10显示了500µs时段的VGS信号波形(短路开始后450µs)。由于100µA的栅极充电电流仍然存在,已经被放电的栅极电压又开始上升。大约130µs后,栅极电压被充分充电(3V),VOUT升至大约1V,这时短路电流再次开始流动。重新充电的过程很慢,足以使快速比较器在电流为33A时触发(200mV/6mΩ),IC将执行关断和闭锁 *** 作。
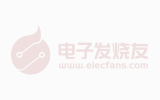
图10. 短路情况下 VGS的时间压缩视图 结论 当热插拔控制电路发生短路故障时,本文讨论的两种电路都可以通过限制功耗来保护背板电源。图2所示的简单电路能够将短路电流持续时间缩短到500ns以内;图3电路稍微复杂些,但可将短路电流限制在100A以内,并且短路电流脉宽小于200ns。
以上任何一种技术都适用于大多数热插拔控制电路。
取决于电源内阻、短路阻抗以及短路故障本身的特性和故障发生时间,个别测试结果会存在一定差异。
欢迎分享,转载请注明来源:内存溢出
评论列表(0条)