本文研究主要考虑基于CuSn金属互化物的微凸点(μbump)作为芯片堆叠的手段。系统研究了形成金属互化物凸点连接的两种方法。一:瞬时液相(TLP)键合,在此过程中,全部Sn焊料熔化,随后通过与焊料盘的作用及凸点下金属化层(UMB)转变为金属间化合物。这些金属间化合物的特点是比焊料本身有更高的熔点。这就可以在对金属间的微连接处没有破坏的情况下进行多芯片连续堆叠、封装构成(倒装芯片,重叠模压)和封装装配。典型的Sn TLP键合温度在240℃以上,高于其熔点232℃。二:固态扩散(SSD)键合,键合温度低于Sn的熔点,一般小于200℃。在此过程中,通过固态交互扩散形成金属间化合物,而不是TLP键合中的液-固反应。另一个不同点是一些未反应Sn可能存在于键合后的连接中。由于SSD键合温度低于Sn的熔点,它不会在较低阶段的堆叠时将焊料连接再熔化,因此也能重复堆叠另外的各层。但金属间各相有望随时间进一步生长,最后将微连接中全部未反应的Sn起反应。
除了Cu/Sn微凸点(μbump)互连外,实现芯片与芯片互连的另一替代方法是基于铟(In)的精细节距焊料凸点。铟是非常软的材料,熔点低(156℃),但成本高,一般局限于高端成像传感器一类的特殊应用。
实验
本文全部实验均用5×5mm2 Imec封装测试芯片进行。图1是晶圆上一些关键测试图形的照片。这些芯片由氧化物介质中的标准单大马士革Cu互连层组成、用氧化物/氮化物层钝化。用于微凸点互连的测试结构主要是菊花链触点的周边行。在一种测试芯片中,它们连接总计480个直径25μm的微凸点连接点,节距为40μm。另一种测试芯片含有8200个直径25μm的微凸点阵列,节距为50μm。微凸点形成工艺是用半加成电镀技术。首先依次淀积TI/Cu籽晶层和光刻胶层。然后进行光刻确定用于微凸点的开口区域。将光刻胶显影后,再依次电镀Cu和Sn,形成微凸点。最后,剥离光刻胶层,将TI/Cu籽晶层刻蚀掉。
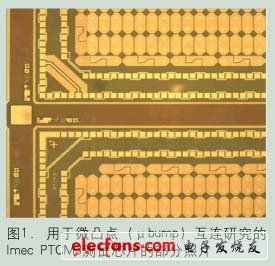
图1所示测试芯片采用60μm周边焊盘节距,并与TSV结合使用。实现这些TSV所用的工艺有详细描述。加工TSV前,把晶圆厚度减至50μm。TSV直径是25μm,深度为50μm。TSV Cu填充和微凸点形成在单一工艺中结合完成。TI/Cu籽晶层在TSV刻蚀后淀积于深宽比为2的50μm TSV上。Cu填充前,应用10μm厚负光刻胶掩膜层,它允许同时形成Cu填充TSV和Cu/Sn凸点。用Cu填充TSV后,直接镀一层3.5μm厚Sn层。光刻胶剥离后,用化学方法除去金属籽晶层。
测试样品的键合在SET FC-150倒装芯片键合机上温度为150-250℃时进行。键合前应用不同的清洗剂(如助溶剂)。键合期间加压(5MPa-150MPa),键合时间3-20分钟。
键合后,测量交织的菊花链的电阻和绝缘以检查互连的电气性能。有些样品还送去做X截面SEM检验。
结果
微凸点由焊料凸点和上芯片上的UBM组成。可焊金属“凸点焊盘”(此例中为Cu)置于下面的衬底上。焊料微凸点的使用也是选项,但本实验未使用。焊料与UBM/可焊金属的反应结果形成金属间化合物,因此上下芯片就连接。本研究中,UBM是Cu或Cu/Ni双金属层,而焊料凸点或包含纯Sn,或包含SnAg。图2是φ25μm微凸点的光学干涉测量剖面,在Cu/Ni UBM上形成了SnAg焊料凸点。
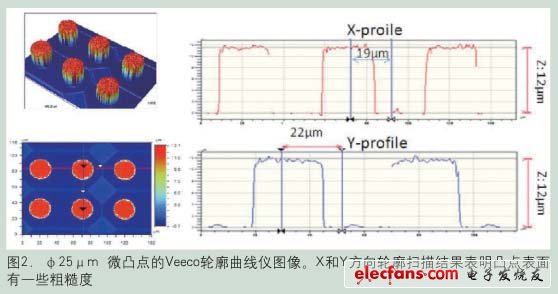
由于Sn和Cu的吉布斯(Gibbs)自由能低,二者均易被氧化。实际上发现,去除氧化物对确保SSD键合的金属间化合物形成至关重要。一些商用清洗剂(如助溶剂)和稀有机酸在倒装芯片键合过程中清洗Cu和Sn。助溶作用也可以用所谓非流动底层填充料(NUF)提供。优点是可与封装装配工艺同时进行底层填充工艺。但它们均不能在很低温度下有效去除氧化物。这使我们的SSD键合温度不能低于150℃。实际上,不同清洗剂的结合给出了150℃时的最佳键合结果。去除氧化物对于TLP键合的重要性不大,此时液态Sn能润湿Cu UBM形成金属间化物。
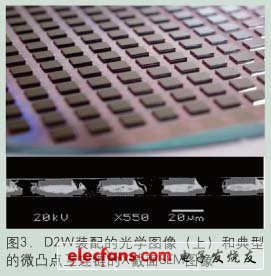
欢迎分享,转载请注明来源:内存溢出
评论列表(0条)