IntroductionPower quality systems monitor in real time and record the voltages and currents from each of three phases of the multiphase power feed from power utilities. These supervisory control and data acquisition (SCADA) systems may also monitor the voltages and currents on the neutral line, thus sensing imbalanced loads or frequency harmonics. Additionally, power-metering systems measure the root mean squared (RMS) voltage and current from each of the three phases to determine power consumption.
Advanced power-line monitoring systems combine power quality, monitoring protection, and metering functions in one system. These systems allow the power utilities and customers to perform predictive maintenance, manage energy consumption and cost, control quality, and protect their equipment—all now performed more efficiently.
Measurement System ArchitectureFigure 1 demonstrates the fundamentals of the AC power measurement by sampling calculations for instantaneous and average power usage. Figure 2 shows a typical power-grid monitoring application. The 3-phase power design shown in Figure 2 refers to three voltages that are offset in phase from each other by 120°, i.e., by one third of a cycle. A fourth wire called neutral is used to accommodate imbalanced loads. If loads on each of the three phases are equal, the system is balanced and no current flows though the neutral line.
This type of the 3-phase power system is standard throughout the world. It is called a wye connection because of the way it appears on a phasor diagram. Each power phase's measurements are represented by a current transformer (CT) and a voltage transformer (PT). The complete system comprises four such pairs (one pair for each of the three phases plus neutral).
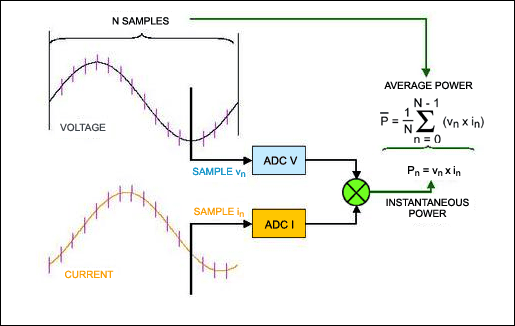
Figure 1. Illustration of AC power measurement by sampling.
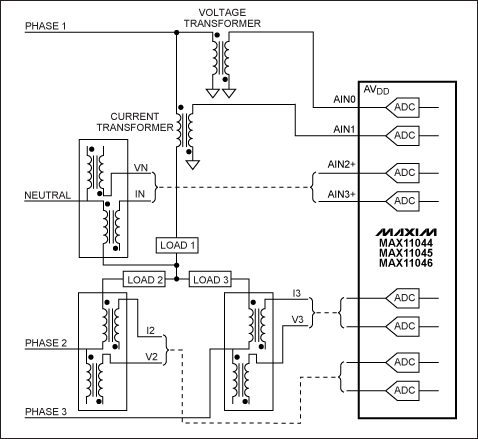
Figure 2. Typical power-grid monitoring application. The wye design is standard throughout the world.
As Figure 2 illustrates, the MAX11044/MAX11045/MAX11046 simultaneously measure the three phases and a neutral voltage plus the currents. By performing digital processing calculations on the sampled and digitally converted data, the active, reactive, apparent energy and power factor parameters can be found. Frequency and harmonic distortion metering can be achieved by performing a Fast Fourier Transform (FFT) on the sampled data.
The measurement characteristics of the delivered energy must comply with international requirements or local standards. An example of international requirements is the European Union (EU) standard EN 50160. Table 1 summarizes the EN 50160 requirements:
Table 1. EN50160 Energy Specifications
Another EU standard, IEC62053, mandates the precision of energy metering equipment. It defines four classes of meters: Class 2, Class 1, Class 0.5, and Class 0.2. (As an example, Class 0.2 requires meter precision to be 0.2% of nominal current and voltage). For power-factor accuracy measurement, phase matching should be 0.1% or better.
For the harmonic voltage, EN 50160 mandates measurement up to the 25th order harmonic of 50Hz/60Hz voltages. However, propagation of the various "nonlinear" loads such as fluorescent lamps and switching power supplies drives measurement up to the 127th order harmonic of 50Hz/60Hz voltages.
Emerging standards like IEC61850 recommend the recording of power-system transient events with 256 samples per AC cycle or higher.
Basic ADC System RequirementsStandards like EN 50160, IEC62053, and IEC61850 dictate both the minimum accuracy and sample rate needed for a modern multichannel ADC system used in power-system monitoring and metering.
Power-monitoring equipment must measure instantaneous current and voltage values with sample rates up to 60Hz x 256 samples, or greater than 15360sps. Moreover, the power monitoring should be capable of measuring power accurately enough to accommodate the IEC62053 standard requirements.
The ADC's dynamic range for voltage measurement can be calculated from the maximum and nominal voltages to be monitored and from the required accuracy for power measurements (see Table 1 and comments on the IEC62053). For example, if a design must measure a 1.5kV (1500V) temporary overvoltage (under a fault condition) with a nominal 220V voltage measurement and a Class 0.2 (0.2%) accuracy requirement, then the total dynamic range of the voltage-measurement subsystem will need to be:
20log ((1500/220) × 2000)) = 83dB
Note: In all the calculations we assumed an intended accuracy of 0.05%, which is substantially below the standard 0.2% accuracy requirements.
Additionally, current-sensing requirements also effect ADC specifications. If the design requirements for power monitoring are the typically 100A:10A (10A nominal and 100A maximum) and Class 0.2 (0.2 %), then the total dynamic range of the current measurement subsystem will need to be:
20log ((100/10) × 2000)) = 86dB
The examples above clearly demonstrate the increasing need for higher performance in ADCs. Today 16-bit resolution at sampling rates of 16ksps, or higher, is essential. To ensure accurate 3-phase and neutral wye system current and voltage measurements, the ADC must be capable of sampling eight channels simultaneously (4 voltage and 4 current), and it must have an excellent SNR of 86dB or better.
Power-Line Monitoring Capabilities of the MAX11046 ADCThe MAX11046 includes eight simultaneous-sampling, low-power, 16-bit, 250ksps, successive-approximation ADCs in a single package. It is ideally suited to power-system monitoring and measurement applications:
An important feature of the MAX11046 is its effective input impedance, ZIN, which is dictated by the input capacitance and sampling frequency:
ZIN = 1/(CIN × Fsample)
Where Fsample is the sampling frequency and CIN = 15pF.
As the sampling frequency drops, input impedance increases:
266kΩ at 250ksps
2.66MΩ at 25ksps
This feature allows the MAX11046 to interface directly with measurement transformers; no external buffer is required.
Figure 3 summarizes the unique benefits of the MAX11046.
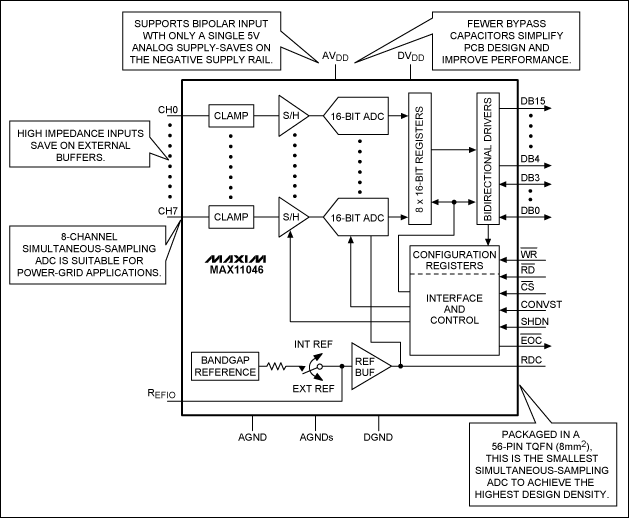
Figure 3. Description of the unique capabilities of the MAX11046 for power-measurement monitoring.
Figure 4 shows an application example generated with the MAX11046 evaluation (EV) kit board connected to power-line monitor transformers. The schematic shows the simple cost and space-efficient interface between the power-line transformers and the MAX11046.
The left oscilloscope plot shows the current and voltages from a compact fluorescent bulb, taken from the CT (current) and PT (voltage) transformers. This configuration was used as a load and test example. The software plot at the right shows the results of the CT and PT signals acquisition and reconstruction post digitization.
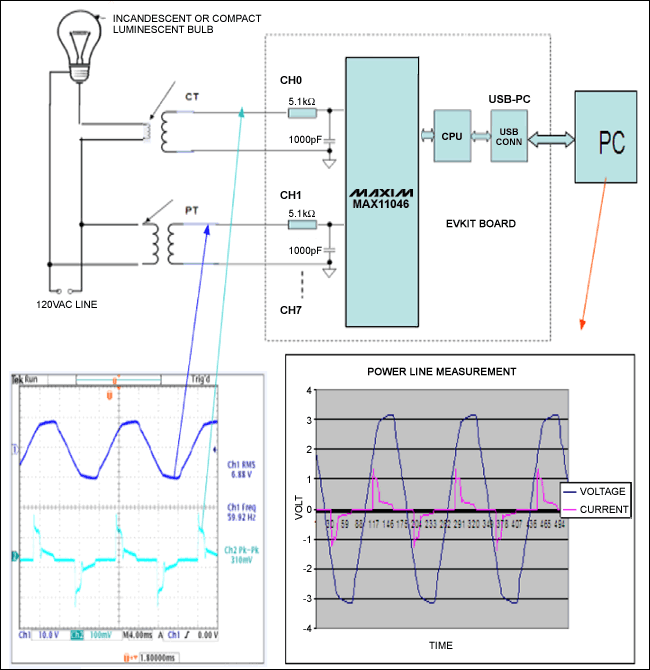
More detailed image (PDF, 759KB)
Figure 4.
ConclusionRising worldwide power demands are driving increased investment in the power-delivery infrastructure. A critical element of these new power delivery systems are multichannel supervisory control and data acquisition (SCADA) systems, which include digital relays for automated power-delivery monitoring, and fault-detection and protection. SCADA systems require multichannel high-resolution ADCs such as MAX11046.
The MAX11046 offers the most efficient 16-bit, 8-channel simultaneous sampling in an 8mm² footprint. It eliminates external buffers due to its high-impedance input structures. The device is optimized for 3-phase power-monitoring and measurement systems, and a natural choice for high-density designs that need to reduce cost and board area while increasing performance.
欢迎分享,转载请注明来源:内存溢出
评论列表(0条)