Anxiety isn't the only influence on breathing patterns; it may be that every feeling affects our respiration. Psychologists investigate these links between emotion and breathing patterns in a number of research areas (Boiten, et al. 1994). Most such investigations require some form of electronic patient-monitoring equipment, partially because the very act of watching one's breathing changes its pattern.
A Respiration Monitor with Smart-Sensor TechnologyThe respiration monitor of Figure 1 displays breathing patterns while giving a rough idea of the respiration amplitude. The monitor displays several important parameters used to detect anxiety: rate of breathing, regularity of breathing pattern, and the duration of pauses after expiration and before inspiration. Because calm, positive emotions usually produce a pattern of longer expiration than inspiration, the ratio of inspiration to expiration time can serve as an additional indicator of anxiety. A relatively higher level of thoracic breathing (vs. abdominal breathing) also indicates anxiety. Thus, an observation of increased thoracic breathing can augment the monitor's visual information.
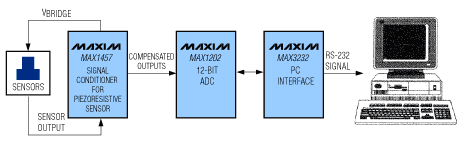
Figure 1. This block diagram depicts a respiration monitor.
Figure 1's monitor uses a silicon piezoresistive transducer (PRT) to detect the decrease and increase of pressure corresponding to inhalation and exhalation. The PRT output is fed to a signal-conditioning IC that corrects for errors inherent in the PRT and then passes a compensated voltage signal to the ADC. The ADC output (a digitized version of the pressure signal) is then fed to a PC interface and converted to RS-232 levels. These in turn are passed to a PC, which displays the respiration waveform and allows analysis of the parameters mentioned above.
The SensorPRTs are commonly configured as a closed Wheatstone bridge. When pressure is applied to an active-bridge PRT (Figure 2a), resistances of the diagonally opposed legs change equally and in the same direction. As the resistances in one set of diagonally opposed legs increase with pressure, the resistances in the other set decrease, and vice versa. A half-active-bridge PRT (Figure 2b) exhibits resistance changes in only half of the bridge. Whether full- or half-active, the advantages of a PRT sensor include high sensitivity (>10mV/V), good linearity at constant temperature, and the ability to track pressure changes without signal hysteresis, up to the destructive limit (Konrad and Ashauer 1999).
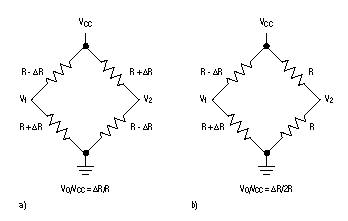
Figure 2. All four legs of an active-bridge PRT (a) respond to pressure. For a half-active-bridge PRT (b), only two legs respond to pressure.
Today's engineers employ PRTs in low- and medium-accuracy applications, but high-end applications have traditionally forced designers to use strain gauges instead—despite their higher cost. New IC technologies that allow accurate PRT sensor correction, however, enable the use of these devices in high-end applications as well.
Sensor ErrorsThe chief obstacle in correcting PRT sensors is the wide range of error magnitude they exhibit. The variety of methods by which PRT sensors are manufactured produces various types of error and a range of error magnitudes. Even for a given model from one manufacturer, these error magnitudes vary appreciably from one transducer to the next.
PRT errors can include ". . . strong nonlinear dependence of the full-scale signal on temperature (up to 1%/°K), large initial offset (up to 100% of full scale or more), [and] strong drift of offset with temperature. Within limits, these disadvantages can be compensated with electronic circuitry" (Konrad and Ashauer 1999).
At a given temperature, both PRT types in Figure 2 maintain their bridge resistance (between VCC and ground) at a level that is fairly constant over a wide range of pressures. As temperature increases, however, the bridge resistance increases significantly. If the bridge is powered with a constant-current source, the result is an increasing bridge voltage.
PRT sensitivity increases as the bridge voltage gets larger with temperature. With bridge voltage held constant, however, a PRT's sensitivity to pressure decreases with temperature. Thus, sensitivity is a function of two opposing factors: temperature and the temperature-dependent bridge voltage. This change in bridge resistance or bridge voltage can be exploited by modern signal-conditioning ICs to correct the sensitivity error over temperature in a PRT. These ICs use the change of bridge resistance to correct for variations in sensitivity vs. temperature.
A Traditional Correction SchemeThe Figure 3 circuit compensates PRTs to a reasonable accuracy level. It allows adjustment of offset, offset drift with temperature, and sensitivity drift with temperature. Related to sensitivity drift is the full-span output drift over temperature; these two parameters change proportionally in response to temperature. Figure 4 shows the relationship between offset and full-span output.
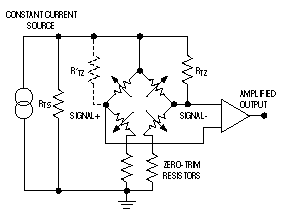
Figure 3. A traditional correction scheme for PRTs features temperature-sensitive resistors.
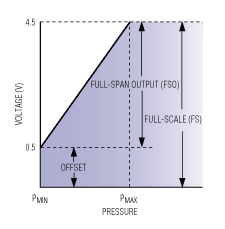
Figure 4. A PRT's offset and full-span output constitute the full-scale output.
The circuit's zero-trim resistors compensate the sensor's offset voltage at room temperature, and resistors RTS and RTZ (or R´TZ) correct for temperature errors. As described earlier, bridge resistance rises with increasing temperature, which increases the voltage across the sensor. That additional voltage increases the sensor's sensitivity; i.e., its output voltage is higher for a given pressure.
When the voltage across the sensor is held constant, however, the sensor's sensitivity decreases with increasing temperature. Because the positive-going sensitivity coefficient caused by increasing bridge resistance with temperature is greater than the negative-going sensitivity coefficient, the full-span output tends to increase with temperature. Resistor RTS negates this effect by shunting increasing amounts of bridge current as temperature rises. Similarly, RTZ or R´TZ correct the offset drift. Depending on the direction of the offset drift with temperature, either RTZ or R´TZ is added to the circuit.
The chief problem with this compensation scheme is circuit interaction among the compensation components, which makes calibration cumbersome and limits the achievable accuracy. Also, electronic trimming is not feasible when using this technique.
A Modern Correction SchemeIn Figure 5, a signal-conditioning IC (MAX1457) drives the respiration monitor's sensor and corrects the sensor errors. It contains a controlled current source that drives the sensor and an ADC that digitizes the sensor's bridge voltage. This voltage is a product of current from the current source and the temperature-dependent bridge resistance.
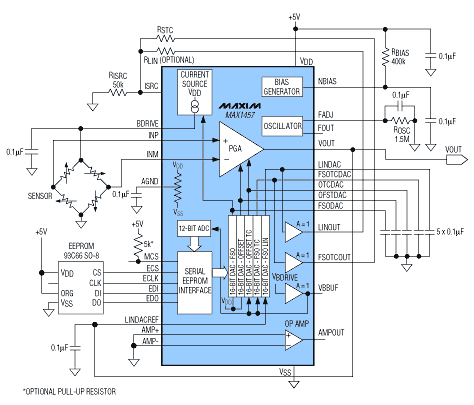
Figure 5. A specialized IC (MAX1457) that provides current-source excitation and compensation for the pressure sensor yields 0.1% accuracy.
The MAX1457 also includes a programmable-gain amplifier (PGA) for amplifying the sensor's differential output and five digital-to-analog converters (DACs) for correcting various sensor errors. Because the sensor output is a low-level signal, the PGA output voltage is not sufficient to drive the ADC. For that reason, the MAX1457's internal op amp is used to boost the PGA output to a suitable level.
Bridge voltage increases with temperature, and this temperature dependence can be used to compensate full-span temperature errors. With constant-voltage bridge excitation, the full-span output (FSO) decreases with temperature, resulting in a full-span output temperature coefficient (FSOTC) error. However, if the bridge voltage can be made to increase with temperature at a rate that compensates for the decrease in full-span sensitivity with temperature, the FSO will remain constant.
Figure 6 shows how the MAX1457 implements this scheme for correcting FSO errors due to temperature. Using the digitized bridge voltage from the ADC output, the chip determines which previously calculated correction coefficient (stored in EEPROM) should be applied to the FSOTC DAC. The resulting DAC output voltage then changes the current level feeding the bridge. This new current level compensates the FSO by adjusting the bridge voltage to compensate the change in sensor sensitivity at a particular temperature. To smooth this correction, the chip applies analog bridge voltage to the FSOTC DAC's reference input, thereby providing an additional correction between each successive pair of digital numbers (supplied by the ADC to the EEPROM).
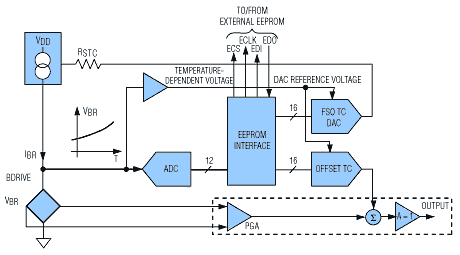
Figure 6. This circuitry within the MAX1457 compensates for offset and full-span temperature errors.
The same technique compensates offset over temperature, except the OFFSETTC DAC voltage is fed to a summing junction at the PGA output (instead of the MAX1457 current source).
Calculate temperature coefficients and store them in EEPROM in the following sequence: in most instances, take sensor data at various pressures with the sensor and MAX1457 at the lowest temperature, then take the same data with the sensor and MAX1457 at the highest temperature. Using this data from the temperature extremes, software written for the MAX1457 then calculates the four correction coefficients (FSO, FSOTC, Offset, and OffsetTC). These four coefficients correct the PRT's first-order errors. (For the accuracy level this respiration monitor requires, a fifth coefficient to correct pressure nonlinearity is considered unnecessary.)
To achieve 0.1% accuracy, the MAX1457 allows compensation at specific temperatures, with recalculation of FSOTC and OffsetTC at each temperature. The user determines the number of such calibration points (up to 120). If sensor output error were perfectly repeatable, the accuracy of a sensor-MAX1457 combination would be better than 0.1%.
The MAX1457 compensation technique has a significant advantage over the traditional approach shown in Figure 3. The MAX1457 eliminates interaction between compensation components by separating the offset and span adjustments: it compensates offset at the PGA and separately adjusts the FSO through the current source. Another advantage is the extra accuracy made available by specific adjustments at various temperatures. This method is inherently more accurate than one based on external resistors, whose values cannot compensate the sensor precisely at specific temperatures.
Simpler Compensation ICsThe MAX1457 provides more precision than necessary for a respiration monitor; i.e., the 16-bit resolution of its correction DACs is more than required. The part was chosen, however, because it includes the extra op amp needed to boost the respiration monitor's low-level sensor signals.
Although the MAX1457 offers greater precision than needed for this application, its ability to compensate for temperature error is needed even for modest variations of temperature: a change of 10°C commonly produces a 3% change in the FSO of a PRT. Because the MAX1457 enables the respiration monitor to operate over a wide temperature range, the monitor's potential applications could include space exploration and scuba diving.
The functions performed by a MAX1450 signal conditioner (Figure 7) are essentially those of a MAX1457, but resistors rather than DACs are used to set the error correction. Because the MAX1450 uses far fewer calibration points than the MAX1457, its accuracy is 1% instead of 0.1%. MAX1450 chips are commonly included in hybrids, where the combination of a MAX1450 and laser-trimmed resistors provides a low-cost solution.
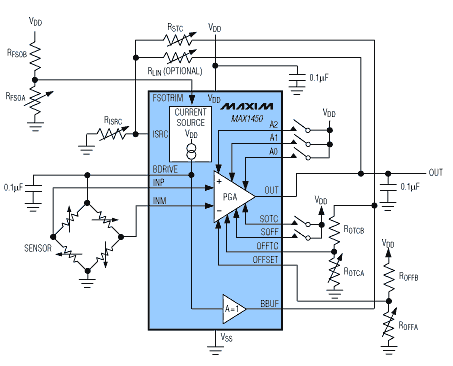
Figure 7. A MAX1450 signal conditioner operating with external laser-trimmed resistors provides 1% accuracy.
A third IC (the MAX1458/MAX1478 of Figure 8) provides the same basic compensation techniques as the other two, but includes 12-bit (vs. 16-bit) compensation DACs. MAX1458/MAX1478 devices also include an EEPROM for on-board storage of the compensation coefficients. Like the MAX1450, they provide 1% accuracy.
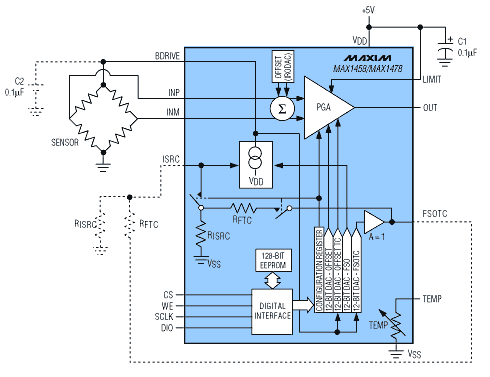
Figure 8. A MAX1458/MAX1478 signal conditioner operating with internal 12-bit DACs provides 1% accuracy.
MAX1450/MAX1458/MAX1478 devices compensate a sensor by calculating four correction coefficients (mentioned above), using pressure data measured at two temperatures—usually the extremes of the operating-temperature range. Unlike these devices, the MAX1457 allows additional temperature-error correction at user-selected temperature levels (as many as 120). For a more detailed discussion of these compensation schemes, refer to Konrad and Ashauer 1999, and Dancaster, et al. 1997.
A similar article was presented at the Sensors Expo in Cleveland, Ohio, September 14-16, 1999.
References
- Boiten, Frans A., Nico H. Frijda, and Cornelius J. E. Wientjes. 1994. Emotions and respiratory patterns: review and critical analysis. International Journal of Psychophysiology 17: 103-128.
- Dancaster, John, Mark Bowen, and Ali Rastegar. 1997. Enhanced performance silicon pressure sensors for automotive applications. Society of Automotive Engineers (reprinted from Sensors and Actuators, 1997): 59-65.
- Fesmire, Steven A. 1994. Aerating the mind: the metaphor of mental functioning as bodily functioning. Metaphor and Symbolic Activity 9 (1): 31-44.
欢迎分享,转载请注明来源:内存溢出
评论列表(0条)