1 电源模型在设计中的应用
电池仿真在产品开发各个进程中都起着重要作用, 尤其在汽车行业的产品设计和试制阶段。设计阶段又可分成系统设计中的系统模型仿真与电源自身个体级数学模型的建立。
1.1 系统设计级模型仿真应用
在汽车供电系统设计中, 传统的设计方法是,根据Feather (市场配置表) 与目标市场气候条件、发动机转速概率落点等一系列因素进行经验性静态估计, 成车后再进行发电机、起动机、蓄电池的动态电量匹配试验分析。
供电系统的仿真模型最为核心的就是蓄电池模型, 蓄电池仿真变量较多, 而且比发电机等其它部件更易受环境影响。图1为汽车供电系统的一个简易模型图( 系统级模型)。
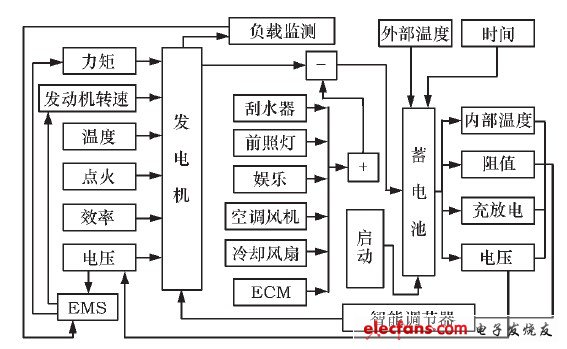
图1 汽车供电系统简易模型图
在欧洲, 许多开发者已开始着手进行系统级仿真的工作, 比如LABCAR ( 整车全仿真试验室) 的建立, SIMULINK模块化发动机模型的建立。此模型输出各种仿真工况下温度和发动机转速等一系列环境参数, 而BCM ( 车身控制器) 等ECU采用半仿真来检测此设计方案。JAGUAR ( 捷豹) 等企业也应用了模型仿真设计方式, 为每一个车系平台都针对车身电子建立一个整车模型系统, 主要进行总线和网络的仿真测试及供电系统的仿真。这些厂商一般使用的是DSPACE发动机模型或teLUS数学模型,而这些模型主要目的大多不是进行供电系统的仿真开发, 而是进行CAN总线的一些开发。在中国, 仅上汽/RICARDO2010在进行这项工作( 供电模型仿真) .在欧洲, 仅德国某整车企业是真正从蓄电池供电系统仿真的开发流程进行开发的。
图2为德国某企业的5系平台的部分供电系统仿真试验结果图。可见仿真的效果很好, 和上汽复测的真实结果吻合得很好。
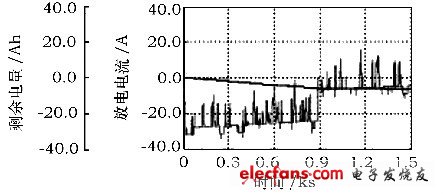
图2 德国某企业5系平台的部分供电系统仿真试验结果图
根据模型的复杂度分别求出电量系统的匹配情况, 可以计算出: 蓄电池、发电机、起动机的容量及选用策略是否合适, 用户电池的更换频率评估,各种不利工况对蓄电池活性物质的影响, 怠速等策略标定是否得当, 发电机失效状态下的供电系统破坏性验证, 静态电流及车辆放置时间测定, 单位电功率与油耗影响关系, 冷起动性能等一系列重要参数。针对以上这些问题, 上汽首先提出供电系统级模型与个体模型的概念, 图3为两者关系图。
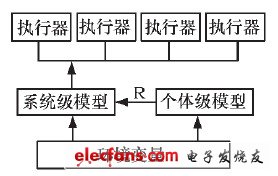
图3 供电系统级模型与个体级模型的关系
图3 反映了汽车供电/蓄电池模型的关系, 个体级模型( 即蓄电池自身变化情况) 根据车型设计复杂度要求含有充放电实时模型、SOC模型、电流实时积分、电压、内阻、水耗、静态放电、电解液密度等各种模型, 环境变量为温度、用户负载、时间等。根据变量输入, 个体级模型会输出一个数组R, 含有蓄电池和整车用电实时状况信息; 系统级模型根据其输入执行各种策略,比如强制关闭负载、怠速短时间提速、进入跛行保护、增加发电机输出、空调补偿调节、用户指示报警、热性能管理、电池安全监测与控制等。
在上汽荣威750轿车上, 笔者在某ECU中少量植入了一些系统级模型, 在不同的使用个体级参数风险评估等级下执行不同的策略。在后续的上汽车型项目中, 笔者也会不同程度地烧录供电模型进行量产化, 并且在未来会使用独立供电模块( JAGUAR已实现量产) , 尤其是上汽未来的中高档轿车。
早期的系统级模型是一个非常简单化的模型:
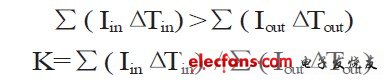
式中: Iin, Iout---分别是在ΔT内的蓄电池平均充放电电流; K---优化系数。
此模型于1998年由大众与VALEO在中国提出,根据优化需要程度, 整车厂对函数K进行赋值 *** 作,其只反映"电要够用"的这一简单道理。此模型过度依赖于原始设计制定的参数, 而没有任何d性,实行了"宁愿最保险"的设计原则, 这样的设计理念对整车企业成本领先的策略是很不利的, 并且没有实时性, 至今大部分中国整车厂或多或少地正在使用此模型, 而上汽提出的系统级与个体级模型彻底解决了这些问题。2001年BMW与ROVER提出新的电量匹配模型标准已具有系统级模糊概念, 加入了系统失效的测试与策略。2006 年上汽与RICARDO2010联合提出的新的电量匹配标准, 突破了蓄电池自身模型参数极限值的局限, 废除了K值的约束, 肯定了系统级的作用。
1.2 个体产品设计级的模型仿真应用
系统级的MATLAB/SIMULINK模型常常是基于所有产品个体级模型的基础上的。
对于蓄电池的开发和设计, 产品个体的仿真模型显得更为重要。但是搭建一个真正的研发用电池环境的成本要远小于建立数学模型, 蓄电池的各种配件相当便宜, 上汽集团的电池供应商大部分都未采用模型、试制、模型优化、量产的循环流程。其实比如风帆、江森自控这样的厂商都有很强的自制零部件的实力, 关键测试的时间虽然比模型用时要长, 但是综合起来节约了总成本, 而且对产品的衍生系列开发和整车厂做供电集成工作有很大帮助。
另一方面, 蓄电池是一个很复杂的系统, 内部各种变量都影响着其容量性能、瞬态输出、水耗、循环次数等。这些变量( 例如: 活性物质的数量、电解液密度和温度、内阻特性、隔板与板栅结构、化学元素的组成、电解质分层特性等) 不同的侧重点会有不同的模型。图4为电池内部复杂的温度分度, 可见电池温度并不是单一参数, 而是对反应源距离间的一个复杂函数, 这也是对传统电池常常提到均衡充电的原因。
图4 电池内部复杂的温度分度示意图
正因为其复杂性, 所以对于各种试验环境下表现出的性能难以从经验预知, 特别是对整车厂开发新产品/车系平台设计来说, 是相当严酷而且耗时的测试, 鉴定试验时间平均半年左右, 一旦试验不成功, 整改和重做的成本是相当大的。因此, 在试验前期常常需要一个前期的"摸底式"测试, 这时仿真测试是最佳选择。而且利用模型可以把电流密度、极板腐蚀、寿命等不论从时间还是技术上难以测量的变量变得更易于测量。这种数学模型系统一旦建立起来后, 新项目开发耗时与成本将会大大减少。图5为使用和未使用该方式开发的耗时区别, 每块为一个完整的开发周期。
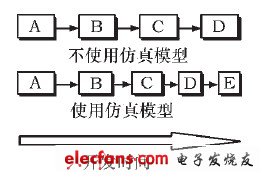
图5 使用和未使用仿真模型开发的耗时区别
欢迎分享,转载请注明来源:内存溢出
评论列表(0条)