本文着眼于微控制器 (MCU) 在工业自动化中的作用,特别是研究它们如何为传感器和执行器提供真实世界的接口。它讨论了将高性能内核(如 ARM® 的 Cortex™-M3)与精密和专用外设(如 Analog Devices 的ADuCM360和 EMF32系列。它还研究了针对该应用领域的相对较新的协议,具体参考了低端 MCU,包括英飞凌的 XC800和 XC16x 系列以及德州仪器的 MSP430F2274,以及包括Maxim 的 MAX14821在内的专用收发器。
微控制器集成了越来越多的混合信号能力和处理能力,但其他发展正在延长低端微控制器的生命周期。
根据定义,微控制器 (MCU) 是冗余的,没有与“现实世界”的接口。它们旨在充当输入和输出的中心,执行条件响应并管理顺序和并行流程。它们的角色由控制定义,而它们的可编程特性意味着控制由逻辑管理。然而,它们基本上被设计为模拟世界的接口,因此严重依赖模拟/数字转换。通常是模拟参数的数字表示——通常来自某种传感器——驱动控制过程,这并不比在自动化应用中更明显。
精确的性能
商业压力意味着对其 *** 作至关重要的数据转换过程必须在片上进行经济高效的处理,从而提高混合信号集成的水平。此外,随着集成度的提高,核心的处理负担也随之增加。
它们的低成本和灵活性意味着 MCU 经常被自由使用,但出于成本、复杂性或安全原因,各行各业的制造商现在都在努力整合功能;曾经可能有数十个 MCU,现在可能只有一个。
因此,从最初的简单 4 位设备演变为高度复杂的 32 位处理引擎也就不足为奇了,其中 ARM Cortex-M 系列成为许多供应商的核心选择。
将高性能处理内核与精确稳定的模拟转换混合在一起并不简单。CMOS 非常适合高速数字,但实例化敏感的模拟外设可能是一个挑战。在这一领域拥有丰富专业知识的公司之一是 ADI 公司。其 ADuCM 系列完全集成的数据采集系统旨在直接连接到精密模拟传感器。这种方法不仅可以最大限度地减少组件数量,还可以通过消除模拟和/或数字级来保持精度。
例如,在基于 ARM Cortex-M3 的 ADuCM360 上实现的转换器是一个 24 位 Sigma Delta ADC,它构成了设备模拟子系统的一部分。其中包括一个可编程电流激励源和一个偏置电压发生器,但更重要的是内部滤波器,其中一个用于精密测量,一个用于快速测量,适用于检测源信号的大变化。
深度睡眠感应
MCU 制造商认识到传感器在自动化中发挥的重要作用,并开始开发优化的模拟前端,为电感、电容和电阻传感器提供专用接口。
其中一些前端甚至设计为自主运行,例如 Energy Micro 超低功耗 MCU 系列中的 LESENSE(低功耗传感器)接口。它包括模拟比较器、DAC(数模转换器)和低功耗定序器,允许它由 MCU 的内核进行配置,然后在设备的其余部分处于深度睡眠模式时运行。
定序器从 32 kHz 时钟运行并控制活动,而比较器输出可配置为中断以唤醒 CPU,DAC 可选择作为比较器参考和激励源。LESENSE 技术还包括一个可配置的解码器,可配置为仅在同时满足多个传感器条件时才生成中断。Digi-Key 提供 Energy Micro 的 EFM32 TIny Gecko 入门套件,其中包括 LESENSE 演示。Energy Micro 的 TIny Gecko 系列 MCU 基于 ARM Cortex-M3,运行频率高达 32 MHz,面向温度、振动、压力和运动传感等工业自动化应用领域。

图 1:Energy Micro 的低能耗传感器接口 LESENSE 为工业控制和自动化系统提供灵活的传感器接口。
IO-Link
功能强大的新型传感器和执行器接口的推出正在帮助许多制造商延长工业自动化领域中 8 位和 16 位设备的使用寿命。接口背后的协议称为 IO-Link,并且已经得到工业自动化领域的许多领导者的支持,尤其是 MCU 供应商。
IO-Link 使用 3 线非屏蔽电缆,最长可达 20 米,适合将智能传感器和执行器改装到现有装置中。它在每一端都需要“智能”,通常在 MCU 中实现,但由于协议相对简单,它可以容纳在低成本的 8 位 MCU 中,这正是许多制造商现在正在开发的。
该协议(也称为 SDCI,代表单点数字通信接口,并根据 IEC 61131-9 规范进行标准化)已被开发为可轻松嵌入传感器和执行器中的点对点通信解决方案,给他们一定程度的“智力”。因此,它并不打算取代现有的通信层,如现场总线、Profinet 或 HART,而是通过使低成本 MCU 更容易与高精度传感器和执行器接口来与它们一起工作。
IO-Link 背后的联盟相信它可以显着降低系统复杂性,并引入有用的功能,例如通过参数监控进行实时诊断。当通过网关(同样,通过 MCU 或 PLC 实现)集成到现场总线拓扑中时,可以从控制室集中监控和管理复杂的系统。传感器可以远程配置,部分原因是符合 IO-Link 规范的传感器比“常规”传感器更了解自身。
首先,他们的身份(和制造商的)以 XML 形式嵌入传感器中,在询问时可用。这允许系统立即计算传感器,并了解它可以为系统做出什么贡献。但是,更重要的是,IO-Link 使传感器(和执行器)能够向控制器提供连续的实时数据流。事实上,IO-Link 提供了三种类型的数据交换:过程数据、服务数据和事件。过程数据是循环传输的,而服务数据是非循环交换的,并且始终应 IO-Link 主站的请求。服务数据可用于从/向设备读取和写入参数数据。
IO-Link 为 MCU 与智能传感器的接口提供了一种更简单的方式,使系统工程师能够开发更智能的工业自动化解决方案。
许多 MCU 供应商已加入 IO-Link 联盟,该联盟最近成为 PI(PROFIBUS 和 PROFINET 国际)内的技术委员会 (TC6)。从根本上说,IO-Link 为控制器(包括 MCU 和 PLC)提供了一种标准化方法,用于识别、控制并与采用该协议的传感器和执行器进行一般通信。提供兼容设备的制造商名单正在增加,MCU 制造商的支持也在增加。
部分支持来自专家,例如德国设计公司 Mesco Engineering,该公司正与多家半导体制造商合作开发 IO-Link 解决方案。其合作伙伴名单包括英飞凌、意法半导体、爱特梅尔和德州仪器。例如,英飞凌已将 Mesco 的 IO-Link 堆栈移植到其 XC800,这是一款兼容 8051 的 8 位 MCU,可在链路的设备(传感器/执行器)端提供智能,而英飞凌正在为 IO-Link 提供支持Master 使用它的 16 位设备,包括 XE16x。
Mesco 的堆栈也已移植到德州仪器的低功耗 MSP430 系列;另一个基于专有内核的 16 位 MCU。具体来说,它以 MSP430F2274 为目标。
制造商还致力于开发一系列分立式 IO-Link 收发器,例如 Maxim 的 MAX14821。该收发器以 IO-Link 设备和 24 V 二进制传感器/执行器为目标,并充当运行数据链路层协议的 MCU 的物理层接口(图 3)。两个内部线性稳压器在 5 V 和 3.3 V 下产生共同的传感器和执行器电源要求,并且该设备通过 SPI 接口进行配置和监控。它还具有一个 IO 收发器接口,能够在高达 36 V 的电压下工作。
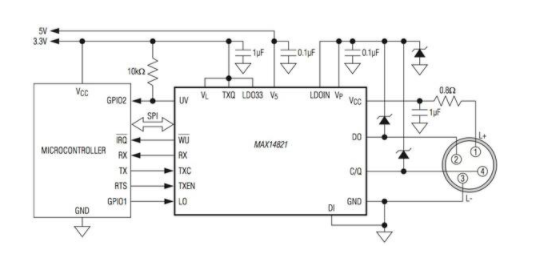
图 :Maxim 的 IO-Link 收发器为运行数据链路层协议的 MCU 提供物理层接口。
随着 IO-Link 实现更高水平的渗透,似乎有更多制造商将这些物理接口与针对工业自动化应用的 MCU 上的其他专用外设集成。瑞萨电子已经基于其 78 K 16 位 MCU 内核创建了一系列专用 IO-Link 主/从控制器。
工业自动化一直依赖于测量和控制的结合。尽管近年来引入了越来越多的网络,但数字域和模拟域之间的接口保持相对不变。然而,随着 IO-Link 的引入,现在正在开发能够以更复杂的方式与 MCU 连接的传感器和执行器。点对点连接不仅提供了一种更简单的控制元件接口方式,而且还提供了一种扩展低端 MCU 功能的有效方式。
欢迎分享,转载请注明来源:内存溢出
评论列表(0条)